Method for preparing lignocellulose aerogel by using ionic liquid
A technology of lignocellulose and ionic liquids, applied in the field of preparation of lignocellulose airgel, can solve the problems of out-of-shape macroscopic rubber blocks and complicated raw material processing, and achieve the effects of broadening applications, increasing use value, and reducing costs
- Summary
- Abstract
- Description
- Claims
- Application Information
AI Technical Summary
Problems solved by technology
Method used
Image
Examples
specific Embodiment approach 1
[0015] Embodiment 1: The method for preparing lignocellulose aerogels using ionic liquids in this embodiment is carried out according to the following steps: 1. After the wood is pulverized, it is passed through a 60-200 mesh sieve to obtain wood powder, and the wood powder and ionic liquid are subjected to Vacuum drying, mix 1-4 parts of dried wood flour with 20-80 parts of dried ionic liquid, heat to 80-130°C, stir for 0.5-4 hours to obtain a mixed solution; 2. Then seal the mixed solution into a mold , freeze at -196~-20°C, the freezing time is 2~24h, and then thaw the frozen mixed solution at a temperature 5~40°C higher than the melting point of the ionic liquid for 1~10h; 3. Repeat step 2 1 ~9 times, then add replacement solution I to the mold, the replacement time is 8h, and the number of replacements is 3~8 times to obtain lignocellulose gel; 4. Carry out critical point drying or drying to the lignocellulose gel obtained in step 3 Freeze-drying to obtain lignocellulose ...
specific Embodiment approach 2
[0016] Embodiment 2: This embodiment differs from Embodiment 1 in that the wood described in step 1 is the processing residue of branch wood. Others are the same as in the first embodiment.
specific Embodiment approach 3
[0017] Specific embodiment three: the difference between this embodiment and specific embodiment one or two is that in step one, the wood is pulverized and passed through a 120-mesh sieve. Others are the same as in the first or second embodiment.
PUM
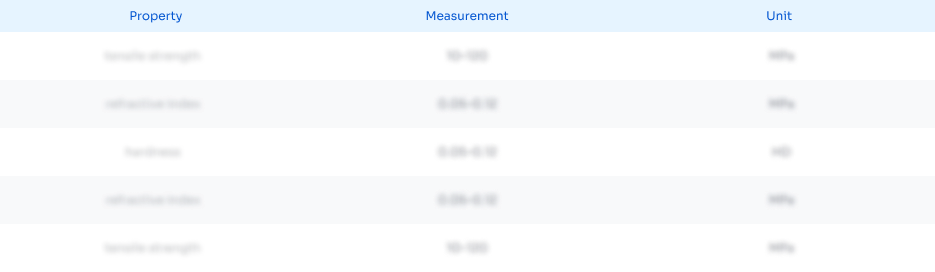
Abstract
Description
Claims
Application Information

- R&D
- Intellectual Property
- Life Sciences
- Materials
- Tech Scout
- Unparalleled Data Quality
- Higher Quality Content
- 60% Fewer Hallucinations
Browse by: Latest US Patents, China's latest patents, Technical Efficacy Thesaurus, Application Domain, Technology Topic, Popular Technical Reports.
© 2025 PatSnap. All rights reserved.Legal|Privacy policy|Modern Slavery Act Transparency Statement|Sitemap|About US| Contact US: help@patsnap.com