Phosphate flame retardant containing styrene structure and synthesis method of phosphate flame retardant
A phosphate ester and styrene technology, which is applied in the field of phosphate ester flame retardants and their synthesis, can solve the problems of low reaction yield, difficult product separation, waste of raw materials, etc., and achieve high reaction yield, easy industrialization, and convenient reaction operation Effect
- Summary
- Abstract
- Description
- Claims
- Application Information
AI Technical Summary
Problems solved by technology
Method used
Image
Examples
Embodiment 1
[0016] Embodiment 1, in the flask equipped with stirring, condensation, drying device, add catalyst sodium hydroxide 0.13g and pyridine 0.49g successively, carbon tetrachloride 6.03g, 4-hydroxystyrene 0.36g, open stirring device, ice Cool in a water bath to 0°C, slowly add a mixture of 0.62g of dibutyl phosphite and 3.52g of carbon tetrachloride dropwise from the dropping funnel, and drop it over in about 2 hours; keep the reaction at 0°C for 42 hours to end the reaction, and filter to form The solid was removed by spinning off the reaction solvent, and the product was separated by column chromatography (ethyl acetate:petroleum ether=2:1) to obtain a sample of 0.90g. The yield is 95.8% (based on 4-hydroxystyrene, the same for the following examples).
Embodiment 2
[0017] Embodiment 2, in the flask equipped with stirring, condensation, drying device, add sodium bicarbonate 0.26g, triethylamine 0.89g, carbon tetrachloride 5.32g, 4-hydroxystyrene 0.36g successively, open stirring device, Cool in an ice-water bath to 5°C, slowly add a mixture of 0.69g of dibutyl phosphite and 4.05g of carbon tetrachloride dropwise from the dropping funnel, and drop it over in 2 hours; keep the reaction at 5-8°C for 36 hours to complete the reaction, and filter to form The solid was spinned off to remove the reaction solvent, and the product was separated by column chromatography (ethyl acetate:petroleum ether=2:1) to obtain sample 0.91. Yield 96.9%.
Embodiment 3
[0018] Embodiment 3, in the four-necked flask that stirring, condensation and drying device are housed, add catalyst sodium carbonate 1.05g and tetrabutylammonium hydroxide 1.25g successively, carbon tetrachloride 6.35g, 4-hydroxystyrene 0.60g, Turn on the stirring device, cool to 3°C in an ice-salt bath, and slowly add a mixture of 0.69 g of diethyl phosphite and 4.37 g of carbon tetrachloride dropwise from the dropping funnel, and the drop will be completed in about 2.5 hours. Keep the reaction at 3-10°C for 40 hours to complete the reaction, filter off the generated solid, spin off the reaction solvent, and separate the product by column chromatography (ethyl acetate:petroleum ether=1:1) to obtain a sample of 1.23g. Yield 96.3%.
PUM
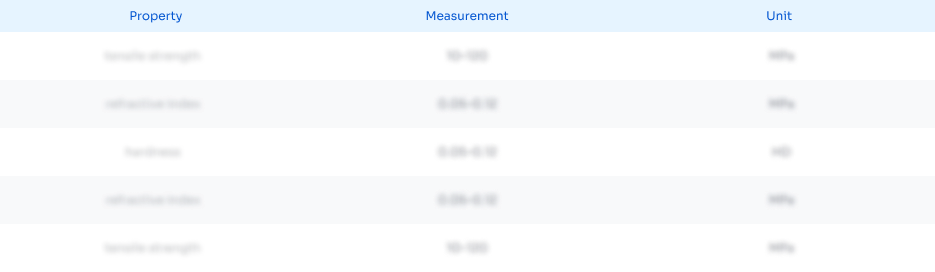
Abstract
Description
Claims
Application Information

- R&D Engineer
- R&D Manager
- IP Professional
- Industry Leading Data Capabilities
- Powerful AI technology
- Patent DNA Extraction
Browse by: Latest US Patents, China's latest patents, Technical Efficacy Thesaurus, Application Domain, Technology Topic, Popular Technical Reports.
© 2024 PatSnap. All rights reserved.Legal|Privacy policy|Modern Slavery Act Transparency Statement|Sitemap|About US| Contact US: help@patsnap.com