New method for welding ZL203 aluminum alloy on preset magnesium-based amorphous intermediate layer
A ZL203, amorphous technology, applied in the field of aluminum alloy welding, can solve problems such as no patent publication
- Summary
- Abstract
- Description
- Claims
- Application Information
AI Technical Summary
Problems solved by technology
Method used
Image
Examples
Embodiment
[0015] Cut and saw the self-cast ZL203 aluminum-copper alloy sample into a block with a length of 35mm, a width of 15mm, and a thickness of 15mm. After the oxide film on the surface is smooth and the surface is to be welded, soak it with acetone solution, clean it with an ultrasonic cleaner for 15 minutes, remove oil and other impurities, and then quickly dry it with a hair dryer. In order to ensure that the joints are evenly stressed, the aluminum-copper alloy is welded in the form of a butt joint.
[0016] Diffusion welding of ZL203 aluminum alloy in a resistance furnace under the protection of high-purity argon. After the diffusion welding material is ready, heat up the resistance furnace and keep the heating rate at about 25°C / min. 65 Cu 20 Al 5 Y 10 The alloy is sandwiched between the ZL203 aluminum alloy columnar materials, and then put into the resistance furnace, and the argon gas is passed through for about 2 minutes before putting in, to ensure that the air in th...
PUM
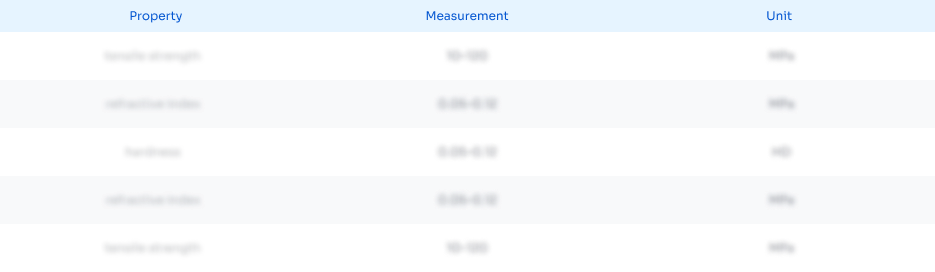
Abstract
Description
Claims
Application Information

- R&D
- Intellectual Property
- Life Sciences
- Materials
- Tech Scout
- Unparalleled Data Quality
- Higher Quality Content
- 60% Fewer Hallucinations
Browse by: Latest US Patents, China's latest patents, Technical Efficacy Thesaurus, Application Domain, Technology Topic, Popular Technical Reports.
© 2025 PatSnap. All rights reserved.Legal|Privacy policy|Modern Slavery Act Transparency Statement|Sitemap|About US| Contact US: help@patsnap.com