Ore dressing technology for treating vanadium titano-magnetite
A vanadium-titanium-magnetite and process technology, which is applied in the field of beneficiation technology for vanadium-titanium-magnetite processing, can solve the problems of high coercivity of vanadium-titanium-magnetite, decreased recovery rate, low final concentrate grade, etc. The effect of lower coercivity and magnetic agglomeration, improved job recovery, and improved grinding efficiency
- Summary
- Abstract
- Description
- Claims
- Application Information
AI Technical Summary
Problems solved by technology
Method used
Image
Examples
Embodiment Construction
[0013] The specific implementation manner of the present invention will be further described below in conjunction with the accompanying drawings.
[0014] Such as figure 2 As shown, a kind of beneficiation process for processing vanadium-titanium magnetite of the present invention comprises the following steps: feeding the crushed raw ore into a ball mill in a closed-circuit grinding and classification, and grinding the particle size to -200 mesh 40%-50 % of the first-stage classification overflow is fed into the roughing magnetic separator, and the tailings of the roughing magnetic separator are the final tailings. Two-stage ball mill, the second-stage ball mill discharges ore and returns to classification, the particle size is ground to -200 mesh 65% to 95%, and the overflow of the second-stage classification is fed into the magnetic separator. The tailings of the magnetic separator are the final tailings, and the magnetic separator concentrate After demagnetization, it is...
PUM
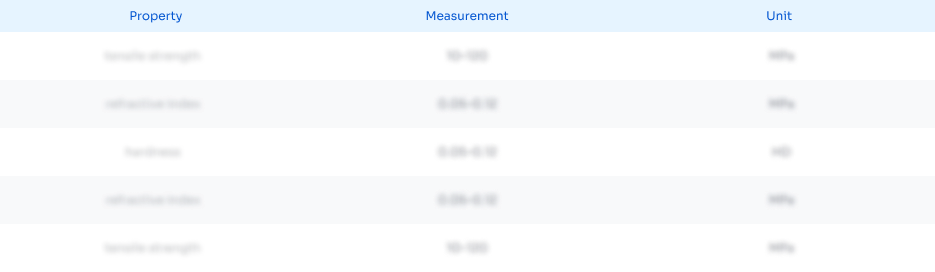
Abstract
Description
Claims
Application Information

- R&D Engineer
- R&D Manager
- IP Professional
- Industry Leading Data Capabilities
- Powerful AI technology
- Patent DNA Extraction
Browse by: Latest US Patents, China's latest patents, Technical Efficacy Thesaurus, Application Domain, Technology Topic, Popular Technical Reports.
© 2024 PatSnap. All rights reserved.Legal|Privacy policy|Modern Slavery Act Transparency Statement|Sitemap|About US| Contact US: help@patsnap.com