Liquid die forging and rolling compound formation method for aluminum alloy irregular-section large ring piece
A liquid die forging, rolling composite technology, applied in metal rolling and other directions, can solve the problem that the comprehensive mechanical properties of metal rings cannot meet the requirements for use of launch vehicles, the processing requirements of complex cross-section rings, and the comprehensive mechanical properties of rings. It can improve the utilization rate of materials, improve productivity and economic benefits, and improve the comprehensive mechanical properties.
- Summary
- Abstract
- Description
- Claims
- Application Information
AI Technical Summary
Problems solved by technology
Method used
Examples
no. 1 example
[0031] The liquid forging-rolling compound forming method of aluminum alloy different cross-section large rings in this embodiment includes the following steps, the aluminum alloy in this embodiment is 6082 aluminum alloy:
[0032] 1) Smelting: smelting 6082 aluminum alloy in a melting furnace according to the composition ratio, and standing for 25 minutes after the smelting is completed; specifically, the raw materials for smelting aluminum alloy in this embodiment are pure aluminum ingots, pure zinc blocks, magnesium blocks, and copper Ingots and intermediate alloys; pure aluminum ingots, pure zinc ingots and magnesium ingots are all sanded with sandpaper before use to remove scale and dirt on the surface, then washed in clean water, and then baked in an electric furnace to remove vapor.
[0033] 2) Liquid die forging: After fixing the liquid die forging die on the indirect squeeze casting machine, pour the aluminum alloy solution obtained in step 1) quantitatively into the ...
no. 2 example
[0047] The liquid die forging rolling compound forming method of the aluminum alloy different cross-section large-scale ring in this embodiment includes the following steps. The aluminum alloy in this embodiment is 6082 aluminum alloy:
[0048] 1) Smelting: smelting 6082 aluminum alloy in a melting furnace according to the composition ratio, and standing for 30 minutes after the smelting is completed; specifically, the raw materials for smelting aluminum alloy in this embodiment are pure aluminum ingots, pure zinc blocks, magnesium blocks, and copper Ingots and intermediate alloys; pure aluminum ingots, pure zinc ingots and magnesium ingots are all sanded with sandpaper before use to remove scale and dirt on the surface, then washed in clean water, and then baked in an electric furnace to remove vapor.
[0049] 2) Liquid die forging: After fixing the liquid die forging die on the indirect squeeze casting machine, pour the aluminum alloy solution obtained in step 1) quantitativ...
no. 3 example
[0063] The liquid die forging rolling compound forming method of the aluminum alloy different cross-section large-scale ring in this embodiment includes the following steps. The aluminum alloy in this embodiment is 6082 aluminum alloy:
[0064] 1) Smelting: smelting 6082 aluminum alloy in a melting furnace according to the composition ratio, and standing for 25 minutes after the smelting is completed; specifically, the raw materials for smelting aluminum alloy in this embodiment are pure aluminum ingots, pure zinc blocks, magnesium blocks, and copper Ingots and intermediate alloys; pure aluminum ingots, pure zinc ingots and magnesium ingots are all sanded with sandpaper before use to remove scale and dirt on the surface, then washed in clean water, and then baked in an electric furnace to remove vapor.
[0065] 2) Liquid die forging: After fixing the liquid die forging die on the indirect squeeze casting machine, pour the aluminum alloy solution obtained in step 1) quantitativ...
PUM
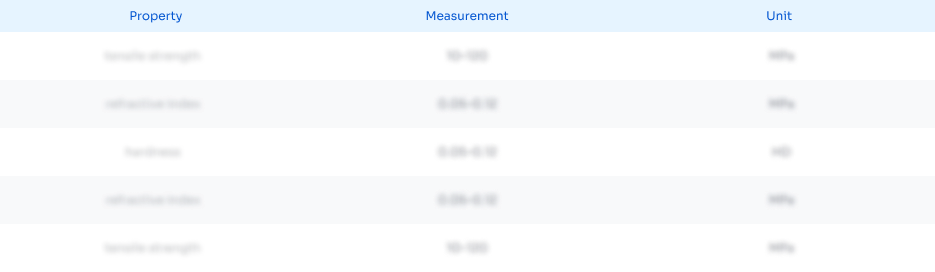
Abstract
Description
Claims
Application Information

- Generate Ideas
- Intellectual Property
- Life Sciences
- Materials
- Tech Scout
- Unparalleled Data Quality
- Higher Quality Content
- 60% Fewer Hallucinations
Browse by: Latest US Patents, China's latest patents, Technical Efficacy Thesaurus, Application Domain, Technology Topic, Popular Technical Reports.
© 2025 PatSnap. All rights reserved.Legal|Privacy policy|Modern Slavery Act Transparency Statement|Sitemap|About US| Contact US: help@patsnap.com