Method and system for simulating feedforward and feedback in heat treated (TRT) blast furnace top pressure cloth control process
A simulation method, feed-forward feedback technology, applied in blast furnaces, blast furnace details, furnaces, etc., can solve problems such as lack of good control solutions, maintenance of top pressure fluctuations, and normal effects of blast furnaces
- Summary
- Abstract
- Description
- Claims
- Application Information
AI Technical Summary
Problems solved by technology
Method used
Image
Examples
Embodiment Construction
[0063] figure 2 It is the top pressure control model diagram of TRT blast furnace, that is, the topological structure of the entire TRT simplified model. Boundary A produces a stable gas flow, which enters the blast furnace through pipe A, and the gas flows out of the furnace top through the material layer in the blast furnace, and passes through a long pipe B flows into the vanes in the turbine and finally flows out to boundary B.
[0064] The material layer of the blast furnace is divided into upper and lower spaces, which can be equivalent to two airtight large containers, namely the upper container and the lower container, while the material layer can be equivalent to a valve, namely the first regulating valve. When the porosity of the material layer is increased, it is equivalent to the process of reducing the opening of the first valve. At this time, the gas volume entering the furnace top through the first valve decreases, causing the pressure on the furnace top to dec...
PUM
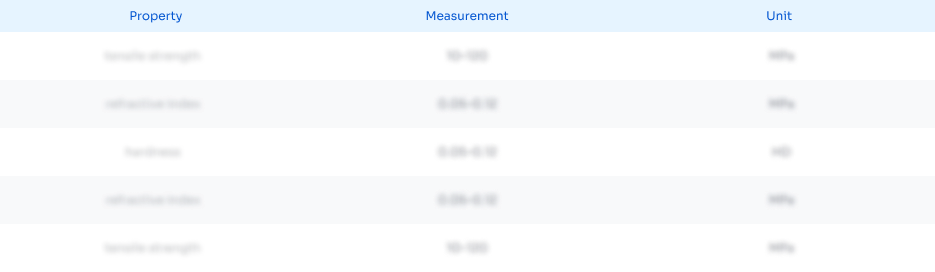
Abstract
Description
Claims
Application Information

- Generate Ideas
- Intellectual Property
- Life Sciences
- Materials
- Tech Scout
- Unparalleled Data Quality
- Higher Quality Content
- 60% Fewer Hallucinations
Browse by: Latest US Patents, China's latest patents, Technical Efficacy Thesaurus, Application Domain, Technology Topic, Popular Technical Reports.
© 2025 PatSnap. All rights reserved.Legal|Privacy policy|Modern Slavery Act Transparency Statement|Sitemap|About US| Contact US: help@patsnap.com