Biodegradable plastic and production method thereof
A technology of biodegradable plastics and production methods, applied in the field of biodegradable plastics, can solve the problems of incomplete combustion, pollute the air, reduce the strength of plastics, etc., achieve the effects of good flexibility and strength, simple preparation method, and prevent coating cracking
- Summary
- Abstract
- Description
- Claims
- Application Information
AI Technical Summary
Problems solved by technology
Method used
Image
Examples
Embodiment 1
[0024] Raw materials: polyethylene resin 60kg, lignocellulose 28kg, 1200 mesh zeolite powder 11.7kg, cellulose degrading enzyme (endo-β-1,4-glucose) 0.3kg.
[0025] Preparation method: add cellulose-degrading enzyme into 1 liter of ethanol and stir evenly, then add zeolite powder into the ethanol solution and mix evenly, remove ethanol under reduced pressure at 40°C, so that the cellulose-degrading enzyme remains in the micropores of the zeolite, and then add Lignocellulose, polyethylene resin, and zeolite powder are mixed, then granulated by a granulator to produce biodegradable plastic, and then the biodegradable plastic is blown to form a film 1 .
[0026] Lignocellulose, zeolite powder and cellulose degrading enzymes were replaced with starch of equal weight to make biodegradable plastics, and a comparative film 1 of the same specification was also made.
[0027] The film 1 and the comparative film 1 were subjected to a strength test and a degradation comparison experiment...
Embodiment 2
[0029] Raw materials: polyethylene resin 65kg, lignocellulose 25kg, 1200 mesh zeolite powder 9.8kg, cellulose degrading enzyme (β-glucosidase) 0.2kg.
[0030] Preparation method: add cellulose degrading enzyme into 1 liter of ethanol and stir evenly, then add zeolite powder into the ethanol solution and mix evenly, remove ethanol under reduced pressure at 40°C, then mix lignocellulose, polyethylene resin, and zeolite powder , and then granulated by a granulator to make a biodegradable plastic, and then the biodegradable plastic is blown into a film 2 .
[0031] The zeolite powder was replaced with talcum powder of equal weight to make a biodegradable plastic, and a comparative film 2 with the same specifications as the film 2 was also made. A strength test and a degradation comparison experiment in 5% water soil showed that the tensile strength of the biodegradable plastic in Example 2 was basically equivalent to that of the comparison film 2, and the degradation time was shor...
Embodiment 3
[0033] Raw materials: 63kg of polyethylene resin, 20kg of lignocellulose, 16.9kg of 1200 mesh zeolite powder, 0.1kg of cellulose degrading enzyme (β-glucosidase).
[0034] Preparation method: add cellulose degrading enzyme into 1 liter of ethanol and stir evenly, then add zeolite powder into the ethanol solution and mix evenly, remove ethanol under reduced pressure at 40°C, then mix lignocellulose, polyethylene resin, and zeolite powder , and then granulated by a granulator to make a biodegradable plastic, and then the biodegradable plastic is blown into a film 3 .
[0035] The cellulose-degrading enzyme was replaced with polyethylene to make a biodegradable plastic, and a comparative film 3 of the same specification was also made. The strength test and the degradation comparison experiment in 5% soil showed that the tensile strength of the biodegradable plastic of Example 3 was basically equivalent to that of the comparison film 3, and the degradation time was shortened by 18...
PUM
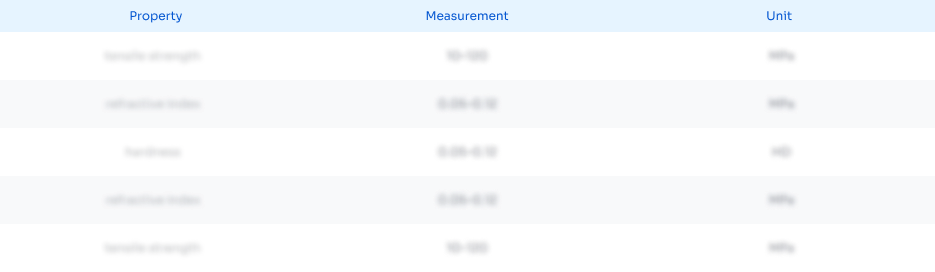
Abstract
Description
Claims
Application Information

- Generate Ideas
- Intellectual Property
- Life Sciences
- Materials
- Tech Scout
- Unparalleled Data Quality
- Higher Quality Content
- 60% Fewer Hallucinations
Browse by: Latest US Patents, China's latest patents, Technical Efficacy Thesaurus, Application Domain, Technology Topic, Popular Technical Reports.
© 2025 PatSnap. All rights reserved.Legal|Privacy policy|Modern Slavery Act Transparency Statement|Sitemap|About US| Contact US: help@patsnap.com