Synthesizing method of epoxy resin by autocatalysis of lignin
A technology of epoxy resin and lignin, which is applied in the field of lignin utilization, can solve the problems of high-boiling alcohol lignin extraction process complexity, low extraction rate, and high cost, so as to create economic value and social value, improve safety, reduce The effect of polluting emissions
- Summary
- Abstract
- Description
- Claims
- Application Information
AI Technical Summary
Problems solved by technology
Method used
Image
Examples
Embodiment 1
[0011] Utilize 20% mass fraction of sulfuric acid solution to adjust the pH of papermaking black liquor to 8.5, filter to remove ash and impurities, and obtain lignin alkali solution; weigh 5.13g of bisphenol A, place it in a 250mL three-necked flask, and transfer it into a 19.6mL ring Oxychloropropane, stirred in a water bath at 50°C until fully dissolved; add 1mL lignin alkali solution to the system as a catalyst, react for 30min, heat up to 90°C, then add 21mL lignin alkali solution to the solution, lignin The addition ratio is equivalent to 10wt.%, and the stirring is stopped after 1 hour of reaction; the product is filtered hot, and the filtrate is collected for vacuum distillation to remove residual moisture and excess epichlorohydrin. Finally, epoxy resin was obtained, which was a brown viscous liquid, and the yield and epoxy value were shown in Table 1.
Embodiment 2
[0013] Utilize 20% mass fraction of sulfuric acid solution to adjust the pH of papermaking black liquor to 8.5, filter to remove ash and impurities, and obtain lignin alkali solution; weigh 4.85g of bisphenol A, place it in a 250mL three-necked flask, and transfer it into a 19.6mL ring Oxychloropropane, stirred in a water bath at 50°C until fully dissolved; add 1mL lignin alkali solution to the system as a catalyst, react for 30min, heat up to 90°C, then add 32mL lignin alkali solution to the solution, lignin The addition ratio is equivalent to 15wt.%, and the stirring is stopped after 1 hour of reaction; the product is filtered hot, and the filtrate is collected for vacuum distillation to remove residual water and excess epichlorohydrin. Finally, epoxy resin was obtained, which was a brown viscous liquid, and the yield and epoxy value were shown in Table 1.
Embodiment 3
[0015] Utilize 20% mass fraction of sulfuric acid solution to adjust the pH of papermaking black liquor to 8.5, filter to remove ash and impurities, and obtain lignin alkali solution; weigh 4.56g of bisphenol A, place it in a 250mL three-necked flask, and transfer it into a 19.6mL ring Oxychloropropane, stirred at 50°C water bath temperature until fully dissolved; add 1mL lignin alkali solution to the system as a catalyst, react for 30min, heat up to 90°C, then add 43mL lignin alkali solution to the solution, lignin The addition ratio is equivalent to 20wt.%, and the stirring is stopped after 1 hour of reaction; the product is filtered hot, and the filtrate is collected for vacuum distillation to remove residual moisture and excess epichlorohydrin. Finally, epoxy resin was obtained, which was a brown viscous liquid, and the yield and epoxy value were shown in Table 1.
PUM
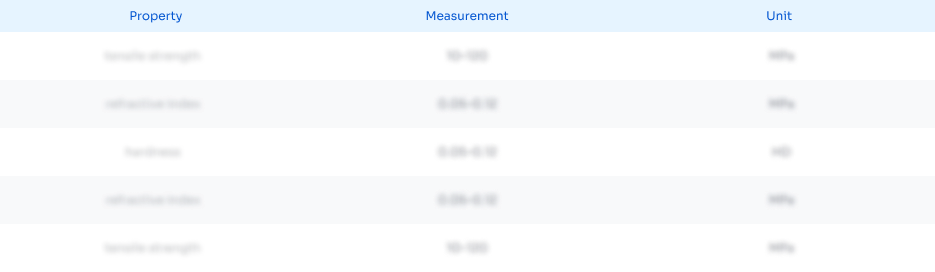
Abstract
Description
Claims
Application Information

- R&D
- Intellectual Property
- Life Sciences
- Materials
- Tech Scout
- Unparalleled Data Quality
- Higher Quality Content
- 60% Fewer Hallucinations
Browse by: Latest US Patents, China's latest patents, Technical Efficacy Thesaurus, Application Domain, Technology Topic, Popular Technical Reports.
© 2025 PatSnap. All rights reserved.Legal|Privacy policy|Modern Slavery Act Transparency Statement|Sitemap|About US| Contact US: help@patsnap.com