Method for producing ADC foaming agent by using chlorine gas-oxidized HDCA (biurea) in saturated hydrochloric acid solution
A technology of ADC foaming agent and hydrochloric acid solution, which is applied in the field of chlorine gas oxidation of HDCA to produce ADC foaming agent, can solve the problems of unutilized, unclean washing, and unstable product quality, so as to save resources, realize recycling, improve The effect of reaction rate
- Summary
- Abstract
- Description
- Claims
- Application Information
AI Technical Summary
Problems solved by technology
Method used
Image
Examples
Embodiment 1
[0025] Weigh 100g of biurea and 30g of water in a 1L reaction kettle, and weigh 30g of saturated hydrochloric acid solution in the reaction kettle, turn on the stirring paddle and stir to make the slurry evenly stirred. Weigh 3gNaBr in the reactor, adjust the reaction temperature to 25°C, open the pipeline for chlorine gas, feed chlorine gas at a rate of 0.1mol / h, and produce hydrazine hydrochloride through the pipeline at the gas outlet into the reactor of hydrazine hydrate. After the reaction, the product ADCA was filtered, washed and dried, and the yield after weighing was 92%, and the reaction rate of hydrazine hydrochloride could be doubled.
Embodiment 2
[0027] Weigh 100g of biurea and 30g of water in a 1L reaction kettle, and weigh 30g of saturated hydrochloric acid solution in the reaction kettle, turn on the stirring paddle and stir to make the slurry evenly stirred. Weigh 5g of NaBr in the reaction kettle, adjust the reaction temperature to 50°C, open the pipeline for chlorine gas, and feed chlorine gas at a rate of 0.3mol / h, and the pipeline at the gas outlet is connected to the reactor of hydrazine hydrate to produce hydrazine hydrochloride. After the end, the product ADCA is filtered, washed and dried, and the yield after weighing is 95%, and the reaction rate of hydrazine hydrochloride can be doubled.
Embodiment 3
[0029] Weigh 100g of biurea and 30g of water in a 1L reaction kettle, and weigh 30g of saturated hydrochloric acid solution in the reaction kettle, turn on the stirring paddle and stir to make the slurry evenly stirred. Weigh 8gNaBr in the reactor, adjust the reaction temperature to 75°C, open the pipeline for chlorine gas, feed chlorine gas at a rate of 0.5mol / h, and produce hydrazine hydrochloride through the pipeline at the gas outlet into the reactor of hydrazine hydrate. After the reaction, the product ADCA was filtered, washed and dried, and the yield was 98% after weighing, and the reaction rate of hydrazine hydrochloride could be doubled.
PUM
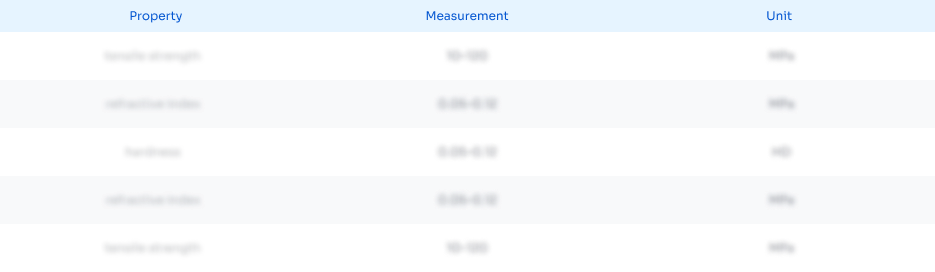
Abstract
Description
Claims
Application Information

- Generate Ideas
- Intellectual Property
- Life Sciences
- Materials
- Tech Scout
- Unparalleled Data Quality
- Higher Quality Content
- 60% Fewer Hallucinations
Browse by: Latest US Patents, China's latest patents, Technical Efficacy Thesaurus, Application Domain, Technology Topic, Popular Technical Reports.
© 2025 PatSnap. All rights reserved.Legal|Privacy policy|Modern Slavery Act Transparency Statement|Sitemap|About US| Contact US: help@patsnap.com