Preparation method of prealloying powder
A technology for pre-alloyed powder and powder, applied in the field of pre-alloyed powder preparation, can solve the problem of high production cost, achieve the effects of high production efficiency, improved thermal efficiency, and no component segregation
- Summary
- Abstract
- Description
- Claims
- Application Information
AI Technical Summary
Problems solved by technology
Method used
Examples
Embodiment 1
[0013] Mix iron powder and copper powder in a ratio of 96:4 (mass ratio), mix them in a three-dimensional mixer for 30 minutes, and then put them into a In the glass tube, add at the other end The red copper electrode is used, and nitrogen gas is passed into the tube for 5 minutes, and the direct current of 200A is connected. It only takes 4.5 seconds to complete, and then crushed and sieved to prepare pre-alloyed powder.
Embodiment 2
[0015] Mix iron powder and copper powder in a ratio of 85:15 (mass ratio), mix them in a three-dimensional mixer for 30 minutes, and then put them into a ceramic tube, add at the other end It only takes 4.8 seconds to complete the red copper electrode with 350A alternating current, and then it is crushed and sieved to prepare pre-alloyed powder.
Embodiment 3
[0017] Mix iron powder, copper powder, and tin powder in a ratio of 75:15:10 (mass ratio), mix them in a three-dimensional mixer for 30 minutes, and then put them into a box with a copper electrode at one end. ceramic tube, add at the other end It takes only 4.3 seconds for the red copper electrode to be connected to 450A alternating current, and then crushed and sieved to prepare pre-alloyed powder.
PUM
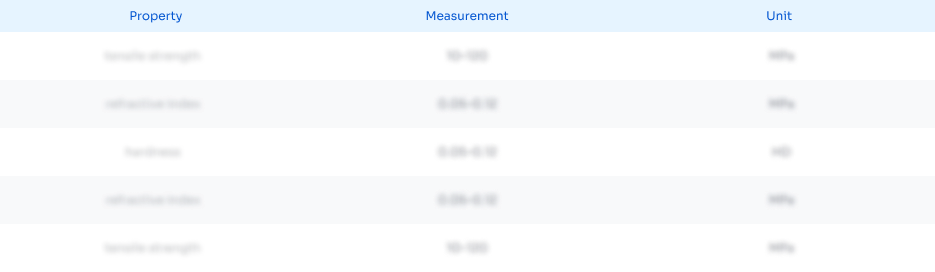
Abstract
Description
Claims
Application Information

- R&D Engineer
- R&D Manager
- IP Professional
- Industry Leading Data Capabilities
- Powerful AI technology
- Patent DNA Extraction
Browse by: Latest US Patents, China's latest patents, Technical Efficacy Thesaurus, Application Domain, Technology Topic, Popular Technical Reports.
© 2024 PatSnap. All rights reserved.Legal|Privacy policy|Modern Slavery Act Transparency Statement|Sitemap|About US| Contact US: help@patsnap.com