Dry grinding and dry concentration method for magnetic minerals
A dry separation method and magnetic technology, applied in chemical instruments and methods, magnetic separation, grain processing, etc., can solve the problems of low separation efficiency, high production cost, low product quality, etc., to overcome low product quality and production cost. Low, high product quality effect
- Summary
- Abstract
- Description
- Claims
- Application Information
AI Technical Summary
Problems solved by technology
Method used
Image
Examples
Embodiment Construction
[0043] The preferred embodiments of the present invention will be described below in conjunction with the accompanying drawings. It should be understood that the preferred embodiments described here are only used to illustrate and explain the present invention, and are not intended to limit the present invention.
[0044] According to an embodiment of the present invention, a method for dry grinding and dry selection of magnetic minerals is provided. Such as figure 1 As shown, this embodiment includes:
[0045] Step 100: After crushing and enriching the ore, use the feeding belt to send the enriched iron ore into the grinding head hoist, and lift it to the grinding head bin through the grinding head hoist; The iron ore in the iron ore is sent to the coarse grinding bin of the dry intermediate unloading ball mill for coarse grinding;
[0046] In step 100, the operation of sending the iron ore in the grinding head bin into the rough grinding bin of the dry-process intermediate u...
PUM
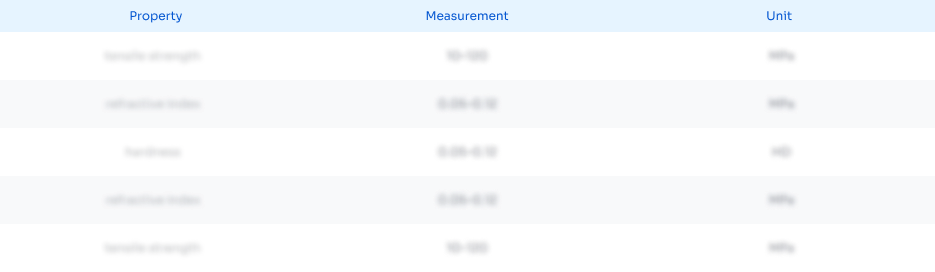
Abstract
Description
Claims
Application Information

- Generate Ideas
- Intellectual Property
- Life Sciences
- Materials
- Tech Scout
- Unparalleled Data Quality
- Higher Quality Content
- 60% Fewer Hallucinations
Browse by: Latest US Patents, China's latest patents, Technical Efficacy Thesaurus, Application Domain, Technology Topic, Popular Technical Reports.
© 2025 PatSnap. All rights reserved.Legal|Privacy policy|Modern Slavery Act Transparency Statement|Sitemap|About US| Contact US: help@patsnap.com