Forward osmosis membrane having high flux for removing salt from sea water and manufacturing method threrof
一种正渗透膜、脱盐的技术,应用在用于海水脱盐的正渗透膜及其制备领域,能够解决减少寿命、分离功能损失等问题,达到防止反向扩散、提高渗水性和水通量、保证耐污染性和化学品耐受性的效果
- Summary
- Abstract
- Description
- Claims
- Application Information
AI Technical Summary
Problems solved by technology
Method used
Image
Examples
preparation example Construction
[0121] The invention provides a method for preparing the forward osmosis membrane used for seawater desalination according to the invention.
[0122] More specifically, a method for preparing a forward osmosis membrane for desalination of seawater is provided, the membrane has a three-layer structure of a nonwoven fabric layer, a hydrophilic polymer layer and a polyamide layer, the method comprising: ( a) forming a hydrophilic polymer layer by coating a solution containing 10 to 25% by weight of a hydrophilic polymer on a nonwoven fabric layer; and (b) forming an organic solution containing a polyfunctional acid halide compound with An aqueous solution containing a polyfunctional amine or an alkylated aliphatic amine is contacted on the hydrophilic polymer layer to perform interfacial polymerization to form the polyamide layer.
[0123]Also provided is a method for preparing a forward osmosis membrane used for seawater desalination, the membrane has a two-layer structure of a ...
Embodiment 1
[0149] A solution containing 17.5 wt% of polyacrylonitrile as a hydrophilic polymer in an organic solvent was cast on a glass plate at a thickness of 50 μm, and then phase-transferred in water used as a non-solvent at room temperature to form a hydrophilic permanent polymer layer. The hydrophilic polymer layer thus obtained was kept in ultrapure water for about one day to extract the solvent. On the surface of the solvent-extracted membrane, an aqueous solution containing 2 wt % m-phenylenediamine (MPD) was interfaced with an organic solution containing 0.1 wt % trimesoyl chloride (TMC) in ISOPAR solvent (Exxon Corp.) In contact, the polyamide layer is formed through the polymerization reaction between these compounds to complete the composite membrane.
Embodiment 2、3 and 4
[0151] These procedures were carried out in the same manner as described in Example 1, except for the membrane composition as given in Table 1, to prepare composite membranes.
PUM
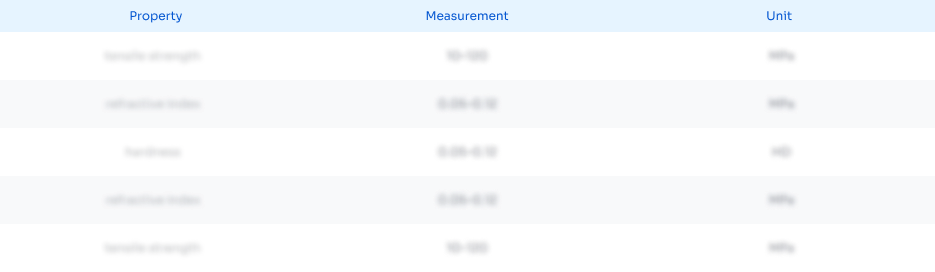
Abstract
Description
Claims
Application Information

- R&D
- Intellectual Property
- Life Sciences
- Materials
- Tech Scout
- Unparalleled Data Quality
- Higher Quality Content
- 60% Fewer Hallucinations
Browse by: Latest US Patents, China's latest patents, Technical Efficacy Thesaurus, Application Domain, Technology Topic, Popular Technical Reports.
© 2025 PatSnap. All rights reserved.Legal|Privacy policy|Modern Slavery Act Transparency Statement|Sitemap|About US| Contact US: help@patsnap.com