Industrial production method of acrylonitrile
A production method and technology of acrylonitrile, applied in chemical instruments and methods, preparation/purification/separation of hydrogen cyanide, chemical recovery, etc., can solve unfavorable system safety and stability, difficulty in wastewater and waste gas treatment, and lack of heat source Make full use of other issues to achieve the effect of improving safety and reliability, saving circulating water and steam, and good economic benefits
- Summary
- Abstract
- Description
- Claims
- Application Information
AI Technical Summary
Problems solved by technology
Method used
Image
Examples
Embodiment 1
[0031] The reaction raw materials liquid propylene and liquid ammonia are mixed into the reactor 1 after passing through the evaporator and the superheater. The other raw material air for the reaction enters the air compressor after being filtered, and also enters the reactor 1 to participate in the reaction after being compressed.
[0032] In reactor 1, propylene, ammonia and air are oxidized under the action of a catalyst to produce acrylonitrile, hydrogen cyanide, acetonitrile, carbon monoxide, carbon dioxide, acrolein, acrylic acid and water. The reaction gas effluent also includes part of unreacted propylene, ammonia, oxygen, nitrogen and the like. The reaction gas enters the cyclone separator in the reactor 1, and the catalyst entrained by the reaction gas returns to the bed layer through the dipleg of the cyclone separator. The reaction gas enters the reaction gas cooler and is sent to the No. 1 tower 2 after being cooled.
[0033]The No. 1 tower 2 is divided into thr...
Embodiment 2
[0041] The reaction raw materials liquid propylene and liquid ammonia are mixed into the reactor 1 after passing through the evaporator and the superheater. The other raw material air for the reaction enters the air compressor after being filtered, and also enters the reactor 1 to participate in the reaction after being compressed.
[0042] In reactor 1, propylene, ammonia and air are oxidized under the action of a catalyst to produce acrylonitrile, hydrogen cyanide, acetonitrile, carbon monoxide, carbon dioxide, acrolein, acrylic acid and water. The reaction gas effluent also includes part of unreacted propylene, ammonia, oxygen, nitrogen and the like. The reaction gas enters the cyclone separator in the reactor 1, and the catalyst entrained by the reaction gas returns to the bed layer through the dipleg of the cyclone separator. The reaction gas enters the reaction gas cooler and is sent to the No. 1 tower 2 after being cooled.
[0043] The No. 1 tower 2 is divided into th...
Embodiment 3
[0051] The reaction raw materials liquid propylene and liquid ammonia are mixed into the reactor 1 after passing through the evaporator and the superheater. The other raw material air for the reaction enters the air compressor after being filtered, and also enters the reactor 1 to participate in the reaction after being compressed.
[0052] In reactor 1, propylene, ammonia and air are oxidized under the action of a catalyst to produce acrylonitrile, hydrogen cyanide, acetonitrile, carbon monoxide, carbon dioxide, acrolein, acrylic acid and water. The reaction gas effluent also includes part of unreacted propylene, ammonia, oxygen, nitrogen and the like. The reaction gas enters the cyclone separator in the reactor 1, and the catalyst entrained by the reaction gas returns to the bed layer through the dipleg of the cyclone separator. The reaction gas enters the reaction gas cooler and is sent to the No. 1 tower 2 after being cooled.
[0053] The No. 1 tower 2 is divided into th...
PUM
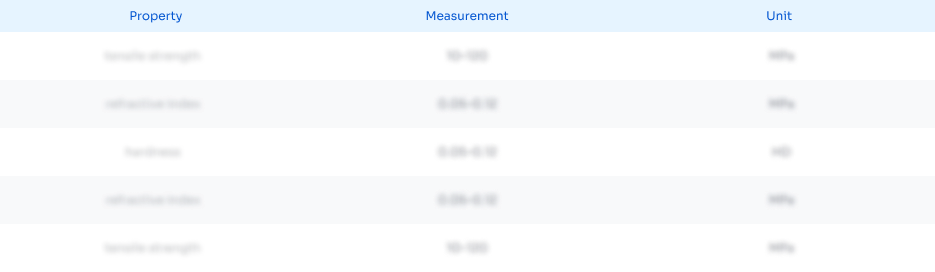
Abstract
Description
Claims
Application Information

- Generate Ideas
- Intellectual Property
- Life Sciences
- Materials
- Tech Scout
- Unparalleled Data Quality
- Higher Quality Content
- 60% Fewer Hallucinations
Browse by: Latest US Patents, China's latest patents, Technical Efficacy Thesaurus, Application Domain, Technology Topic, Popular Technical Reports.
© 2025 PatSnap. All rights reserved.Legal|Privacy policy|Modern Slavery Act Transparency Statement|Sitemap|About US| Contact US: help@patsnap.com