Coaxial drive and control structure for coaxial contrarotation rotor helicopter
A technology of rotor helicopter and coaxial transmission, which is applied to rotorcraft, motor vehicles, transportation and packaging, etc. It can solve the problems of flight accidents, long shaft and rotor length, etc., and achieve the effect of reducing production difficulty and cost and ensuring strength
- Summary
- Abstract
- Description
- Claims
- Application Information
AI Technical Summary
Problems solved by technology
Method used
Image
Examples
Embodiment Construction
[0034] see Figure 1 to Figure 5 and Figure 8 , a coaxial transmission and control structure of a coaxial counterrotor helicopter, comprising a main shaft, an upper rotor hub 3, a lower rotor hub 2, a gear transmission shaft 4, an upper tilter 15, a lower tilter 14, an upper tilter Bracket 12, lower tilter bracket 7, upper synchronous arm 17, lower synchronous arm 16, upper rotor control lever 18a, lower rotor control lever 18b, rotor control arm 23, main pitch control lever 6, total pitch sliding sleeve 5, etc. The main components. The main shaft is a hollow fixed shaft 1 used to support the rotor hub, the lower end of the fixed shaft 1 is fixedly connected to the housing of the reducer 22, and the fixed connection can be fastened by multiple bolts or fixed by multi-point riveting , or fixed by welding. The housing of the speed reducer 22 is fixedly connected on the fuselage of the helicopter, and its fixing method adopts the usual fixed connection method of the helicopte...
PUM
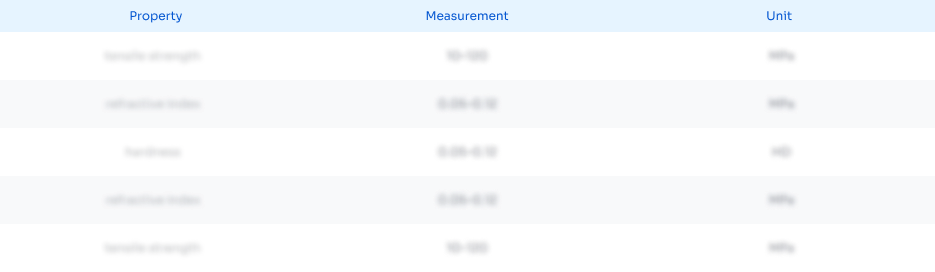
Abstract
Description
Claims
Application Information

- Generate Ideas
- Intellectual Property
- Life Sciences
- Materials
- Tech Scout
- Unparalleled Data Quality
- Higher Quality Content
- 60% Fewer Hallucinations
Browse by: Latest US Patents, China's latest patents, Technical Efficacy Thesaurus, Application Domain, Technology Topic, Popular Technical Reports.
© 2025 PatSnap. All rights reserved.Legal|Privacy policy|Modern Slavery Act Transparency Statement|Sitemap|About US| Contact US: help@patsnap.com