Liquid crystal display panel and manufacturing method and display device thereof
A liquid crystal display panel and display panel technology, which is applied in semiconductor/solid-state device manufacturing, instruments, electrical components, etc., can solve the problems of increasing the battery load of mobile phones, unfavorable display screen light and thin requirements, and large overlap deviation
- Summary
- Abstract
- Description
- Claims
- Application Information
AI Technical Summary
Problems solved by technology
Method used
Image
Examples
Embodiment 1
[0080] combine Figure 1A with 1B shown (where Figure 1A It is a schematic diagram of the top perspective structure of the color filter substrate of the liquid crystal display panel provided in Embodiment 1 of the present invention, Figure 1B Schematic diagram of the structure of the liquid crystal display panel provided by Embodiment 1 of the present invention at the section A-A of the color filter substrate), the liquid crystal display panel provided by the embodiment of the present invention includes a color filter substrate 1 and an array substrate 2, a color filter substrate 1 and an array substrate 2 is filled with liquid crystal (not shown in the figure), the color filter substrate 1 includes: a substrate 10; a color filter layer 11 formed on the substrate and a first insulating layer 13 covering the color filter layer 11, wherein the color filter layer includes The color filter pixel area 12a and the black matrix area 12b; the first conductive signal line 16 formed o...
Embodiment 2
[0087] combine Figure 1C As shown (the schematic diagram of the top view perspective structure of the color filter substrate of the liquid crystal display panel provided by Embodiment 2 of the present invention is the same as that of Embodiment 1, refer to Figure 1A , Figure 1C Schematic diagram of the structure of the liquid crystal display panel provided by Embodiment 2 of the present invention at the section A-A of the color filter substrate), the liquid crystal display panel provided by the embodiment of the present invention includes a color filter substrate 1 and an array substrate 2, and a color filter substrate 1 and an array substrate 2 is filled with liquid crystal, and the color filter substrate 1 includes: a substrate 10; a color filter layer 11 formed on the substrate 10 and a first insulating layer 13 above the color filter layer 11, wherein the color filter layer 11 includes a color filter pixel area 12a and the black matrix region 12b; the first conductive s...
Embodiment 3
[0094] combine Figure 2A and 2B shown (where Figure 2A It is a schematic top view perspective structure diagram of the array substrate of the liquid crystal display panel provided by Embodiment 3 of the present invention, Figure 2B Schematic diagram of the structure of the liquid crystal display panel provided by Embodiment 3 of the present invention at the section A-A of the array substrate), the liquid crystal display panel provided by the embodiment of the present invention includes a color filter substrate 1 and an array substrate 2, and a color filter substrate 1 and an array substrate 2 Liquid crystals are filled between them, and the array substrate 2 includes: a substrate 20; data lines 24 and gate lines 21 that cross vertically and horizontally are formed on the substrate 20; pixel units and TFT switches are formed around the data lines 24 and gate lines 21, wherein the TFT The switch includes a gate electrode, a gate insulating layer 22, a source electrode, a dr...
PUM
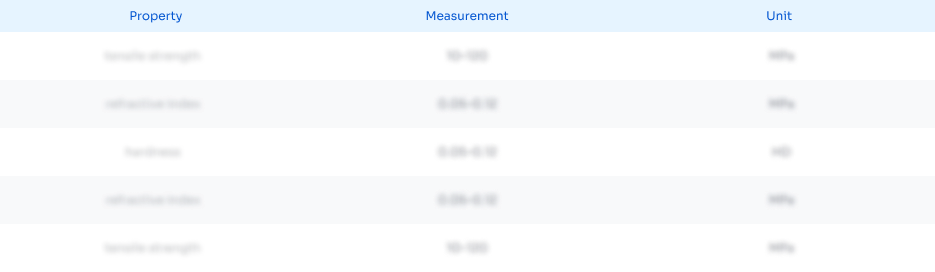
Abstract
Description
Claims
Application Information

- R&D
- Intellectual Property
- Life Sciences
- Materials
- Tech Scout
- Unparalleled Data Quality
- Higher Quality Content
- 60% Fewer Hallucinations
Browse by: Latest US Patents, China's latest patents, Technical Efficacy Thesaurus, Application Domain, Technology Topic, Popular Technical Reports.
© 2025 PatSnap. All rights reserved.Legal|Privacy policy|Modern Slavery Act Transparency Statement|Sitemap|About US| Contact US: help@patsnap.com