Test table for five-function test of driving shaft assembly of constant velocity universal joint
A constant velocity universal joint and functional testing technology, applied in the direction of machine gear/transmission mechanism testing, etc., can solve problems such as affecting the testing accuracy, stepping motor out of step, no explanation, etc., to achieve a wide range of applications, unified testing benchmarks, Measure accurate effects
- Summary
- Abstract
- Description
- Claims
- Application Information
AI Technical Summary
Problems solved by technology
Method used
Image
Examples
Embodiment Construction
[0033] Below in conjunction with accompanying drawing, the embodiment of the present invention is described in detail: present embodiment is carried out on the premise of technical solution of the invention, has provided detailed embodiment and specific operation process, but protection scope of the present invention is not limited to following implementation example.
[0034] Such as figure 1 , 2 As shown, this embodiment includes: frame 1, fixed end guide rail and slider 2, fixed end swing table 3, fixed end linear displacement drive assembly 4, fixed end sliding table 5, fixed end rear support seat 6, torque Speed sensor 7, main shaft support seat 8, main shaft 9, fixed end fixture 10, fixed end screw nut 11, sliding end swing platen 12, sliding end screw nut 13, sliding end fixture 14, sliding end shaft 15, sliding end support seat 16, pull pressure sensor 17, rear sliding plate 18, front sliding plate 19, sliding end guide rail and slider 20, large sliding table plate...
PUM
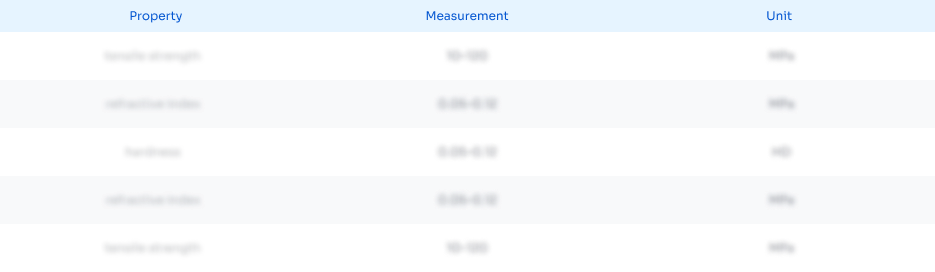
Abstract
Description
Claims
Application Information

- R&D Engineer
- R&D Manager
- IP Professional
- Industry Leading Data Capabilities
- Powerful AI technology
- Patent DNA Extraction
Browse by: Latest US Patents, China's latest patents, Technical Efficacy Thesaurus, Application Domain, Technology Topic, Popular Technical Reports.
© 2024 PatSnap. All rights reserved.Legal|Privacy policy|Modern Slavery Act Transparency Statement|Sitemap|About US| Contact US: help@patsnap.com