Method for producing extra thick composite board through dissymmetrical composite rolling
A composite rolling and asymmetric technology, applied in metal rolling and other directions, can solve the problems affecting the composite quality of the bonding surface, and achieve the effect of improving bonding efficiency and bonding effect, improving deformation, and increasing the degree of recrystallization
- Summary
- Abstract
- Description
- Claims
- Application Information
AI Technical Summary
Problems solved by technology
Method used
Image
Examples
test approach 1
[0040] The thickness of the three-layer billet is 720mm in total, and the 300mm thick plate is produced.
[0041] Prepare three slabs, the thickness is 240mm+240mm+240mm, the total thickness is 720mm, and the composite layer is located at 1 / 3 of the full thickness.
[0042] Surface cleaning is carried out on the combined surfaces of the three slabs, and then vacuum welding is carried out. Put the welded composite billet into the heating furnace and heat it to 1230°C, and start rolling after holding the heat for 5 hours. The rolling start temperature is 1190°C, the reduction range of each pass is 15-30mm, and the final rolling temperature is 1100°C.
[0043] For the composite thick plate after rolling, the flaw detection is carried out according to the "National Standard of the People's Republic of China - Ultrasonic Inspection Method for Thick Steel Plate GB / T 2970-2004", which meets the second-level standard of the national standard.
test approach 2
[0045] The total thickness of the double-layer unequal thickness billet is 720mm, and the thick plate of 360mm is produced.
[0046] In order to compare with the traditional scheme, three groups of composite billets are prepared. There are two steel plates in each group, and the thickness of each steel plate is controlled so that the composite layer is located at different positions in the thickness direction.
[0047] The composite layer of the first group (comparative example) is at 1 / 2 of the full thickness, and the thickness of the two steel plates is 360mm+360mm, that is, the traditional configuration of two steel plates of equal thickness, so as to compare the test results.
[0048] The composite layer of the second group (embodiment) is at 1 / 3 of the full thickness, and the thickness of the two steel plates is 240mm+480mm.
[0049] The composite layer of the third group (embodiment) is located at 1 / 5 of the full thickness, and the thickness of the two steel plates is 1...
test approach 3
[0057] The total thickness of the double-layer unequal thickness billet is 600mm, and it is rolled in a single pass.
[0058] The composite layer of the first group (comparative example) is at 1 / 2 of the full thickness, and the thickness of the two steel plates is 300mm+300mm, which is the traditional configuration of two equal-thickness steel plates, so as to compare the experimental results.
[0059] The composite layer of the second group (the embodiment of the present invention) is at 1 / 3 of the full thickness, and the thickness of the two steel plates is 200mm+400mm.
[0060] The composite layer of the third group (the embodiment of the present invention) is located at 1 / 5 of the full thickness, and the thickness of the two steel plates is 120mm+480mm.
[0061] The above-mentioned groups of steel plates are surface-cleaned and vacuum-welded to form a composite billet. The composite billet is placed in a heating furnace and heated to 1150°C, and then kept for 4 hours befor...
PUM
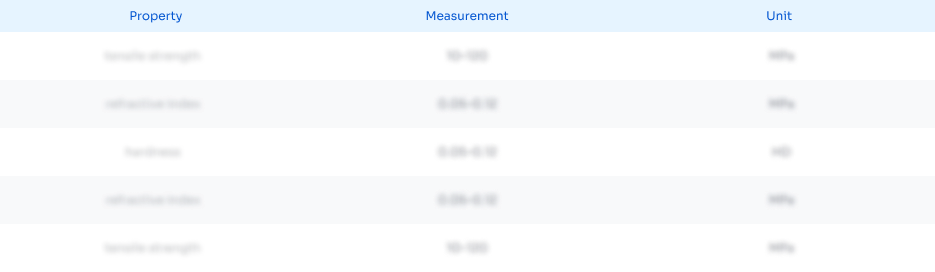
Abstract
Description
Claims
Application Information

- Generate Ideas
- Intellectual Property
- Life Sciences
- Materials
- Tech Scout
- Unparalleled Data Quality
- Higher Quality Content
- 60% Fewer Hallucinations
Browse by: Latest US Patents, China's latest patents, Technical Efficacy Thesaurus, Application Domain, Technology Topic, Popular Technical Reports.
© 2025 PatSnap. All rights reserved.Legal|Privacy policy|Modern Slavery Act Transparency Statement|Sitemap|About US| Contact US: help@patsnap.com