Steckel mill rolled piece head-and-tail deviation control method
A technology of a furnace coil mill and a control method, which is applied in the direction of tail end control, rolling force/roll gap control, etc., can solve the problem that the furnace coil mill cannot roll steel normally, the head and tail of the rolling piece deviate, and the rough rolling intermediate slab cannot be predicted. Status changes, etc.
- Summary
- Abstract
- Description
- Claims
- Application Information
AI Technical Summary
Problems solved by technology
Method used
Image
Examples
Embodiment Construction
[0031] The technical solutions of the present invention will be further described below in conjunction with the accompanying drawings and embodiments.
[0032] see figure 1 As shown, the method for controlling the head and tail deviation of the rolled piece in the steckel mill of the present invention can be carried out by using the existing equipment configuration of the steckel mill production line, wherein, the rough rolling L1 control system is responsible for the equipment control of the rough rolling mill, and collects various parameters of the rough rolling mill. and output the rolling force information on the working side and the operating side of the roughing mill to the deviation control of the steckel mill; Rough Center Line Dispalcement, referred to as RCLD) to control the deviation of the steckel rolling mill; Coil deviation, Steckel CenterLine Dispalcement, referred to as SCLD) is output to the deviation control of the steckel mill; the L2 process machine is res...
PUM
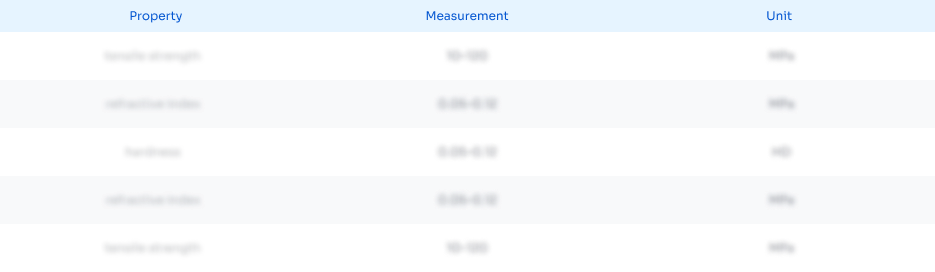
Abstract
Description
Claims
Application Information

- Generate Ideas
- Intellectual Property
- Life Sciences
- Materials
- Tech Scout
- Unparalleled Data Quality
- Higher Quality Content
- 60% Fewer Hallucinations
Browse by: Latest US Patents, China's latest patents, Technical Efficacy Thesaurus, Application Domain, Technology Topic, Popular Technical Reports.
© 2025 PatSnap. All rights reserved.Legal|Privacy policy|Modern Slavery Act Transparency Statement|Sitemap|About US| Contact US: help@patsnap.com