Method for analyzing internal defects of large forge piece
A technology for internal defects and analysis methods, which is applied in the analysis of solids using sonic/ultrasonic/infrasonic waves, testing metals, and material inspection products, etc. It can solve problems such as difficult operation, uneven heating, and inability to fully grasp the performance of material forging and heat treatment. Accurate defect analysis and quality improvement
- Summary
- Abstract
- Description
- Claims
- Application Information
AI Technical Summary
Problems solved by technology
Method used
Image
Examples
specific Embodiment
[0043] Specific examples (such as Figure 6 to Figure 21shown):
[0044] 1) After forging a large square forging with a length of about 5m and a side length of about 2m in cross-section, ultrasonic flaw detection was carried out after initial processing, and it was found that there were a large number of densely distributed cracks in the forging, and the defect equivalent was φ7mm~φ22.5mm. Defect distribution as Image 6 As shown, record the relative position and defect equivalent of internal defects in the forging. In order to determine the nature and cause of flaw detection defects, test rods (that is, sampling) were taken from different defect areas of the forging.
[0045] The test rods were subjected to low-magnification inspection (that is, physical and chemical inspection), and it was found that all the test rods had a crack along the circumferential direction of the test rod at the position where the flaw detection defect was marked, and the crack length was about 10...
PUM
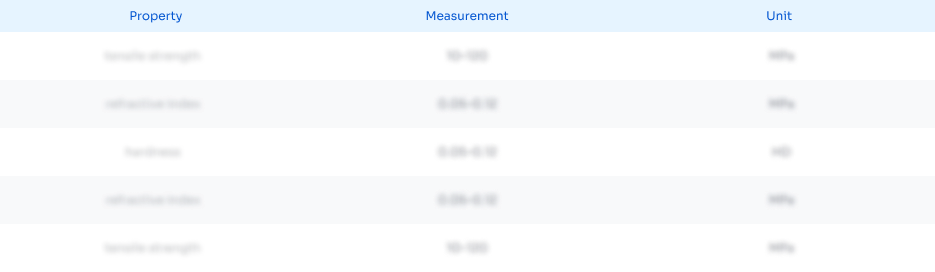
Abstract
Description
Claims
Application Information

- R&D
- Intellectual Property
- Life Sciences
- Materials
- Tech Scout
- Unparalleled Data Quality
- Higher Quality Content
- 60% Fewer Hallucinations
Browse by: Latest US Patents, China's latest patents, Technical Efficacy Thesaurus, Application Domain, Technology Topic, Popular Technical Reports.
© 2025 PatSnap. All rights reserved.Legal|Privacy policy|Modern Slavery Act Transparency Statement|Sitemap|About US| Contact US: help@patsnap.com