Wet spinning cake dyeing process of viscose filament yarns
A technology for silk cake dyeing and viscose filament, which is applied in liquid/gas/steam yarn/filament processing, textile material processing, textile processing machine accessories, etc., which can solve the problems of many broken ends, high production cost and poor quality and other problems, to achieve the effect of improved swelling treatment quality, good sealing performance and uniform density
- Summary
- Abstract
- Description
- Claims
- Application Information
AI Technical Summary
Problems solved by technology
Method used
Image
Examples
Embodiment 1
[0040] A wet silk cake dyeing process for viscose filaments, the process steps include preparing wet silk cakes, loading cylinder sleeves, yarn pressing, creel loading, pre-treatment, dyeing, post-processing and tube forming, characterized in that: The preparation of wet silk cake means that the spun silk cake is pressure-washed and dehydrated to control the moisture content to 50%, and the wet silk cake is obtained without drying; The cylinder cover is put into the yarn column on the yarn disc in the dyeing vat, and the horizontal distance between the outer sides of the wet silk cake on every two adjacent yarn columns is controlled to be 2mm; The cake is completely submerged and the filaments are swelled until the pressure difference between the pressure on the outside of the wet cake and the pressure in the cylinder liner is 1 kg during the internal flow cycle, and the pressure on the outside of the wet cake and the pressure in the cylinder liner during the outflow cycle. Th...
Embodiment 2
[0043] A wet silk cake dyeing process for viscose filaments, the process steps include preparing wet silk cakes, loading cylinder sleeves, yarn pressing, creel loading, pre-treatment, dyeing, post-processing and tube forming, characterized in that: The preparation of the wet silk cake means that the spun silk cake is pressure-washed and dehydrated to control the moisture content to 90%, and the wet silk cake is obtained without drying; The cylinder cover is put into the yarn column on the yarn disc in the dyeing vat, and the horizontal distance between the outer sides of the wet silk cake on every two adjacent yarn columns is controlled to be 50mm; The cake is completely submerged and the filaments are swelled until the pressure difference between the pressure on the outside of the wet cake and the pressure in the cylinder liner is 2kg when the swelling reaches the internal circulation, and the pressure on the outside of the wet cake and the pressure in the cylinder liner are t...
Embodiment 3
[0046] A wet silk cake dyeing process for viscose filaments, the process steps include preparing wet silk cakes, loading cylinder sleeves, yarn pressing, creel loading, pre-treatment, dyeing, post-processing and tube forming, characterized in that: The preparation of wet silk cake means that the spun silk cake is pressure-washed and dehydrated to control the moisture content to 70%, and the wet silk cake is obtained without drying; The cylinder sleeve is put into the yarn column on the yarn disc in the dyeing vat, and the horizontal distance between the outer sides of the wet silk cake on every two adjacent yarn columns is controlled to be 26mm; The cake is completely submerged, and the filaments are swollen. When the swelling reaches the internal flow cycle, the pressure difference between the pressure outside the wet silk cake and the pressure in the cylinder liner is 1.5kg. The pressure difference between the pressures in the jackets was 0.9 kg.
[0047] The pressure diffe...
PUM
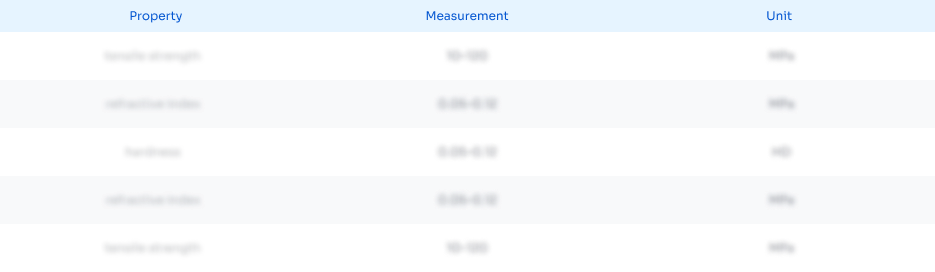
Abstract
Description
Claims
Application Information

- Generate Ideas
- Intellectual Property
- Life Sciences
- Materials
- Tech Scout
- Unparalleled Data Quality
- Higher Quality Content
- 60% Fewer Hallucinations
Browse by: Latest US Patents, China's latest patents, Technical Efficacy Thesaurus, Application Domain, Technology Topic, Popular Technical Reports.
© 2025 PatSnap. All rights reserved.Legal|Privacy policy|Modern Slavery Act Transparency Statement|Sitemap|About US| Contact US: help@patsnap.com