Braze welding heating furnace of aluminum alloy plate-fin heat exchanger and heating partitioning and control methods
A technology of finned heat exchangers and aluminum alloy plates, applied in metal processing equipment, electric heating devices, manufacturing tools, etc., can solve the problems of large fluctuations in product quality, high energy consumption, and a large number of heat exchangers, and achieve excellent The effect of saving performance and good operability
- Summary
- Abstract
- Description
- Claims
- Application Information
AI Technical Summary
Problems solved by technology
Method used
Image
Examples
Embodiment
[0021] Embodiment: The heating space 3 (heating chamber) is an all-metal reflective screen structure, which is butted in sections along the length direction. It is assembled by top suspension and bottom roller positioning to facilitate the installation and maintenance of the heating chamber; The layers of reflective screens are assembled, and the joints are staggered with a certain gap. They are fixed on the stainless steel frame, which can reduce thermal deformation. On the premise of ensuring the internal heat insulation performance of the furnace, the structure is simplified to the greatest extent, and the emission is reduced. Gas volume, so that the vacuum degree in the furnace has been well guaranteed. There is a reasonable space between the heating chamber and the inner wall of the furnace, which is convenient for daily maintenance.
[0022] The main support material of the heating structure is made of 0Cr18Ni9Ti stainless steel, and the heating element is made of Cr20Ni...
PUM
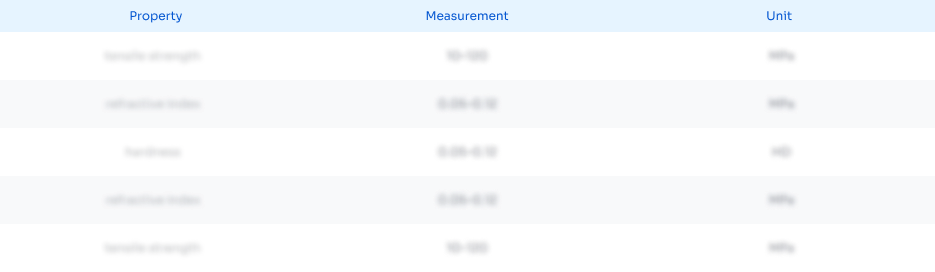
Abstract
Description
Claims
Application Information

- R&D Engineer
- R&D Manager
- IP Professional
- Industry Leading Data Capabilities
- Powerful AI technology
- Patent DNA Extraction
Browse by: Latest US Patents, China's latest patents, Technical Efficacy Thesaurus, Application Domain, Technology Topic, Popular Technical Reports.
© 2024 PatSnap. All rights reserved.Legal|Privacy policy|Modern Slavery Act Transparency Statement|Sitemap|About US| Contact US: help@patsnap.com