An automatic wire feeding jig on a robot welding equipment
A robot welding and wire feeding technology, which is applied in welding equipment, metal processing equipment, tin feeding devices, etc., can solve the problems of heavy physical injury to welding personnel, production efficiency and production volume that cannot meet production needs, and improve welding efficiency Effect
- Summary
- Abstract
- Description
- Claims
- Application Information
AI Technical Summary
Problems solved by technology
Method used
Image
Examples
Embodiment
[0017] Example: see Figures 1 to 5 As shown, an automatic wire-feeding jig on a robot welding device includes a flat wire-feeding box 1, the bottom of the inner side wall on the left and right sides of the wire-feeding box 1 is formed with a slot 11, and the left side of the wire-feeding box 1 A wire feeding nozzle 12 connected with the slot 11 is formed on the outer wall of the side, and a guide groove at the same height as the slot 11 is formed at the bottom of the front end of the wire feed box 1, and the guide groove of the wire feed box 1 is inserted into the Connected with a shifting block 3, the front end of the shifting block 3 protrudes from the front end of the wire feed box 1 and is screwed on the lead screw 5, the two ends of the lead screw 5 are hinged on the support 4, and the support 4 is fixed on the wire feed box On the left and right sides of 1, a wire feed motor 6 is fixedly connected to the support 4 on the left side of the wire feed box 1, and the rotatin...
PUM
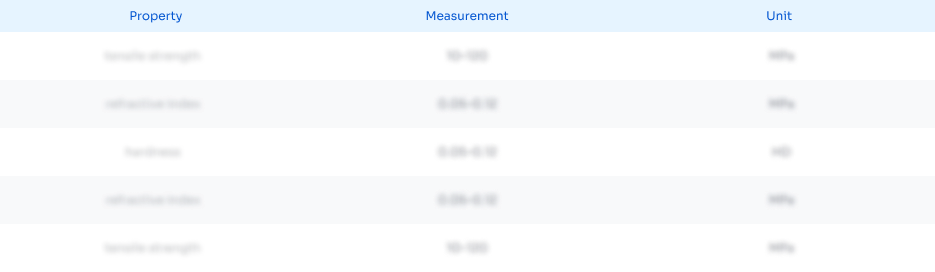
Abstract
Description
Claims
Application Information

- R&D Engineer
- R&D Manager
- IP Professional
- Industry Leading Data Capabilities
- Powerful AI technology
- Patent DNA Extraction
Browse by: Latest US Patents, China's latest patents, Technical Efficacy Thesaurus, Application Domain, Technology Topic, Popular Technical Reports.
© 2024 PatSnap. All rights reserved.Legal|Privacy policy|Modern Slavery Act Transparency Statement|Sitemap|About US| Contact US: help@patsnap.com