Tester and method for testing test environment controllable multi-directional fine motion fatigue
A fretting fatigue, test environment technology, applied in the direction of testing wear resistance, using stable tension/pressure to test material strength, measuring devices, etc. Performance and life, use and maintain accurate results
- Summary
- Abstract
- Description
- Claims
- Application Information
AI Technical Summary
Problems solved by technology
Method used
Image
Examples
Embodiment 1
[0041] figure 1 As shown, a specific embodiment of the present invention is a multi-directional fretting fatigue testing machine with controllable test environment, including a multi-directional fretting fatigue test bench, and the top plate of the support 15 of the multi-directional fretting fatigue testing bench 15A is equipped with an electromagnetic excitation actuator 3 that can move vertically, and the electromagnetic excitation actuator 3 is connected to the upper clamp 5 that clamps the spherical upper test piece 6 through the load cell 4; the lower part of the upper clamp 5 is the clamping The lower fixture of the test piece 7 under the plane, the side of the lower fixture 9 is connected to the piezoelectric ceramic actuator 11 through the force sensor 2 10, and the piezoelectric ceramic actuator 11 is connected to the side plate 12A of the vertical and horizontal two-dimensional mobile platform 12 The bottom of the vertical and horizontal two-dimensional mobile platf...
Embodiment 2
[0051] The multi-directional fretting fatigue testing machine with controllable test environment in this example is exactly the same as that in Example 1. The test method of this example is also basically the same as the method of embodiment 1, and the difference is only:
[0052] In the control of the test environment in step b, the environment control operation of humidity is also carried out, that is, water vapor is introduced into the atmosphere control space through the water vapor inlet 37, so that the atmosphere in the atmosphere control space reaches the set humidity.
Embodiment 3
[0054] The multi-directional fretting fatigue testing machine with controllable test environment in this example is exactly the same as that in Example 1. The test method of this example is also basically the same as the method of embodiment 1, and the difference is only:
[0055] In the control of the test environment of step b, the environment control operation of the liquid medium is also carried out, that is: stop the liquid outlet pipe 32, and fill the required liquid medium into the liquid medium tank 30 through the liquid inlet pipe 31, so that the liquid medium The liquid surface submerges the contact surface of the spherical upper test piece 6 and the plane lower test piece 7 .
PUM
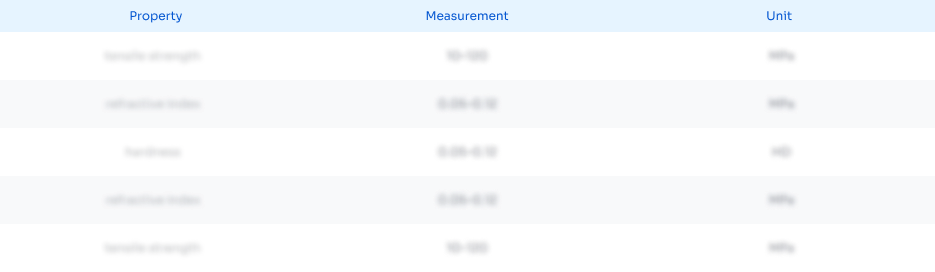
Abstract
Description
Claims
Application Information

- Generate Ideas
- Intellectual Property
- Life Sciences
- Materials
- Tech Scout
- Unparalleled Data Quality
- Higher Quality Content
- 60% Fewer Hallucinations
Browse by: Latest US Patents, China's latest patents, Technical Efficacy Thesaurus, Application Domain, Technology Topic, Popular Technical Reports.
© 2025 PatSnap. All rights reserved.Legal|Privacy policy|Modern Slavery Act Transparency Statement|Sitemap|About US| Contact US: help@patsnap.com