Method for producing iron ore concentrate by quickly burning siderite through microwave
A technology of siderite and iron concentrate, which is applied in the field of microwave rapid calcination of siderite to produce iron concentrate, can solve the problems of large amount of flue gas, high cost, and easy sintering, and achieve high iron ore grade, improved grade, The effect of little pollution
- Summary
- Abstract
- Description
- Claims
- Application Information
AI Technical Summary
Problems solved by technology
Method used
Examples
Embodiment 1
[0018] Place 10Kg of siderite powder with iron content of 40% and moisture content of 0.2% in a microwave reactor, and feed in oxygen according to the mass ratio of oxygen and siderite as 1:18, with a frequency of 2450MHz and an input power of After heating up to 660°C with 3000W, keep it warm for 10 minutes, and stir the siderite powder during the microwave heating and heat preservation process, that is to say, the siderite powder with high grade and the main component is Fe 3 o 4 iron concentrate (56% iron grade).
Embodiment 2
[0020] Place 15Kg of siderite powder with iron content of 40% and moisture content of 0.2% in a microwave reactor, and feed oxygen into the microwave reactor according to the mass ratio of oxygen and siderite as 1:22, with a frequency of 2450MHz and an input power of After heating up to 500°C with 4000W, keep it warm for 30 minutes, and stir the siderite powder during the microwave heating and heat preservation process, that is to say, the siderite powder with high grade and the main component is Fe 3 o 4 iron concentrate (58% iron grade).
Embodiment 3
[0022] Put 100Kg of siderite powder with an iron content of 41% and a moisture content of 0.2% in a microwave reactor, add 7Kg of limonite, and pass in oxygen according to the mass ratio of oxygen and siderite as 1:20, with a frequency The temperature is 2450MHz, and the input power is 14KW. After heating up to 600°C, keep it warm for 60 minutes, and stir the siderite powder during the microwave heating and heat preservation process, that is to say, the siderite powder with high grade and main component is Fe 3 o 4 iron concentrate (58% iron grade).
PUM
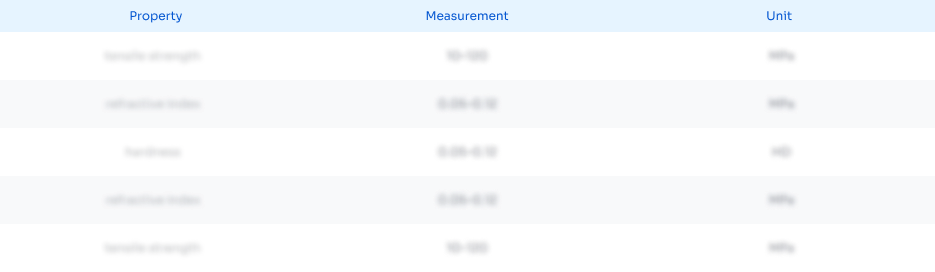
Abstract
Description
Claims
Application Information

- Generate Ideas
- Intellectual Property
- Life Sciences
- Materials
- Tech Scout
- Unparalleled Data Quality
- Higher Quality Content
- 60% Fewer Hallucinations
Browse by: Latest US Patents, China's latest patents, Technical Efficacy Thesaurus, Application Domain, Technology Topic, Popular Technical Reports.
© 2025 PatSnap. All rights reserved.Legal|Privacy policy|Modern Slavery Act Transparency Statement|Sitemap|About US| Contact US: help@patsnap.com