Polypropylene modified material and method for preparing plastic inner casing of water heater by using same
A modified material, polypropylene technology, applied in the field of water heater plastic liner, polypropylene modified materials, can solve the problems of low strength, short service life, easy deformation and aging, etc., to achieve high strength, long service life and easy operation Effect
- Summary
- Abstract
- Description
- Claims
- Application Information
AI Technical Summary
Problems solved by technology
Method used
Examples
Embodiment 1
[0054] 1) Put the raw materials into a mixer according to the mass percentage of 60% polypropylene, 20% glass fiber, 5% calcium carbonate, 5% diphenylamine, 5% carbon black, and 5% sizing agent, and mix for 2 hours at 20°C;
[0055] 2) hot melt:
[0056] Put the mixed material into the hot-melt pipe, and heat-melt at 150°C for 2 hours;
[0057] 3) Extrusion:
[0058] The hot-melted material is fed into the screw extruder and extruded at 100°C with an extrusion pressure of 2MPa;
[0059] 3) Blow molding:
[0060] The extruded material was blow-molded by a blow-molding machine head at a blow-molding temperature of 100° C. and a pressure of 2 MPa to obtain a plastic liner.
Embodiment 2
[0062] 1) Put the raw materials into a mixer according to the mass percentage of 90% polypropylene and 10% glass fiber, and mix for 10 hours at 80°C;
[0063] 2) hot melt:
[0064] Put the mixed material into the hot-melt pipe, and melt it at 200°C for 10 hours;
[0065] 3) Extrusion:
[0066] The hot-melted material is fed into the screw extruder, and extruded at 200°C, with an extrusion pressure of 5MPa;
[0067] 3) Blow molding:
[0068] The extruded material was blow-molded by a blow-molding machine head at a blow-molding temperature of 200° C. and a pressure of 5 MPa to obtain a plastic liner.
Embodiment 3
[0070] 1) Put the raw materials into a mixer according to the mass percentage of 80% polypropylene, 10% glass fiber, 2.5% calcium sulfate, 2.5% pentaerythritol ester, 2.5% zinc oxide, and 2.5% sizing agent, and mix at 60°C for 8 hours;
[0071] 2) hot melt:
[0072] Put the mixed material into the hot-melt pipe, and melt it at 180°C for 8 hours;
[0073] 3) Extrusion:
[0074] The hot-melted material is fed into the screw extruder and extruded at 150°C with an extrusion pressure of 4MPa;
[0075] 3) Blow molding:
[0076] The extruded material was blow-molded by a blow-molding machine head, the blow-molding temperature was 150° C., and the pressure was 4 MPa to obtain a plastic liner.
PUM
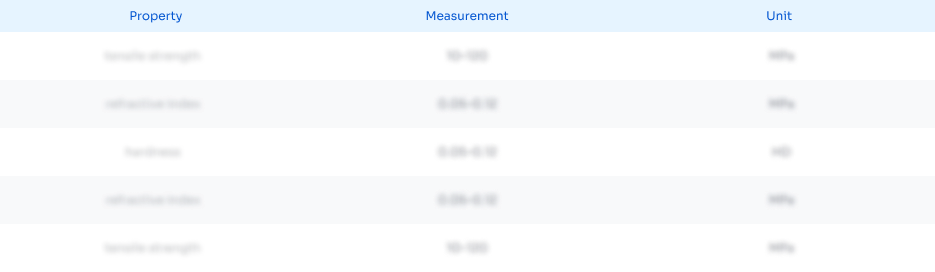
Abstract
Description
Claims
Application Information

- R&D Engineer
- R&D Manager
- IP Professional
- Industry Leading Data Capabilities
- Powerful AI technology
- Patent DNA Extraction
Browse by: Latest US Patents, China's latest patents, Technical Efficacy Thesaurus, Application Domain, Technology Topic, Popular Technical Reports.
© 2024 PatSnap. All rights reserved.Legal|Privacy policy|Modern Slavery Act Transparency Statement|Sitemap|About US| Contact US: help@patsnap.com