Method for preparing epoxy chloropropane by cyclizing dichloropropanol in microreactor
An epichlorohydrin and microreactor technology, applied in the chemical industry, organic chemistry, sustainable manufacturing/processing, etc., can solve the problems of reduced reaction yield, high local alkali concentration, intensified hydrolysis reaction, etc. High yield, high selectivity, and the effect of increasing effective concentration
- Summary
- Abstract
- Description
- Claims
- Application Information
AI Technical Summary
Problems solved by technology
Method used
Examples
Embodiment 1
[0016] Carry out experiment according to this method, preparation solution A, containing dichloropropanol concentration is 2wt.%, hydrogen chloride concentration is 0, preparation solution B, containing sodium hydroxide concentration is 2wt.%, both flows are respectively 20ml / min and 6.2 ml / min, the ratio of the molar ratio (hydroxide / (dichloropropanol+hydrogen chloride)) to 1 is passed into the membrane dispersion micro-reactor, the temperature of the reaction system is 90°C, the two-phase fluid in the reaction equipment The dwell time is 10s. The product was analyzed, and the conversion rate of the reaction reached 98%, and the selectivity reached 99.4%.
Embodiment 2
[0018] Carry out experiment according to this method, preparation solution A, containing dichloropropanol concentration is 5wt.%, hydrogen chloride concentration is 1.4wt.%, preparation solution B, containing sodium hydroxide concentration is 10wt.%, both flows are respectively 20ml / min and 7.4ml / min, the molar ratio (hydroxide / (dichloropropanol+hydrogen chloride)) is 1.2 into the membrane dispersion microreactor, the temperature of the reaction system is 70 ° C, the two-phase fluid is reacting The dwell time in the device is 100s. The product was analyzed, and the conversion rate of the reaction reached 99%, and the selectivity reached 98.3%.
Embodiment 3
[0020] Carry out experiment according to this method, preparation solution A, containing dichloropropanol concentration is 10wt.%, hydrogen chloride concentration is 2.8wt.%, preparation solution B, containing sodium hydroxide concentration is 5wt.%, both flows are respectively 20ml / min and 24.6ml / min, with the ratio of molar ratio (hydroxide / (dichloropropanol+hydrogen chloride)) being 1, it is passed into the micro-sieve reactor, the temperature of the reaction system is 40°C, and the two-phase fluid is in the reaction equipment The dwell time in is 600s. The product was analyzed, and the conversion rate of the reaction reached 98%, and the selectivity reached 96.3%.
PUM
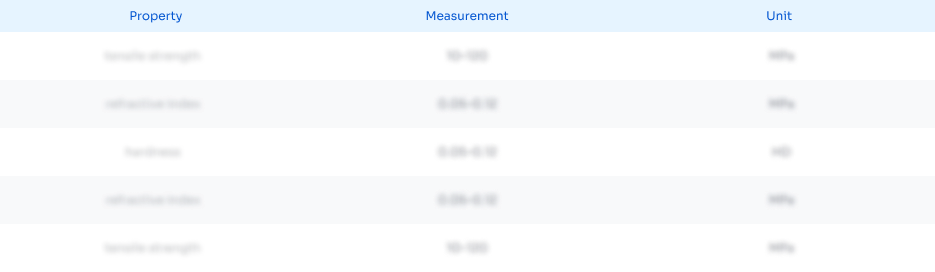
Abstract
Description
Claims
Application Information

- R&D
- Intellectual Property
- Life Sciences
- Materials
- Tech Scout
- Unparalleled Data Quality
- Higher Quality Content
- 60% Fewer Hallucinations
Browse by: Latest US Patents, China's latest patents, Technical Efficacy Thesaurus, Application Domain, Technology Topic, Popular Technical Reports.
© 2025 PatSnap. All rights reserved.Legal|Privacy policy|Modern Slavery Act Transparency Statement|Sitemap|About US| Contact US: help@patsnap.com