Preparation method of reticular multi-component composite oxide monolithic denitration catalyst
A denitration catalyst and multi-component composite technology are applied in the field of preparation of a network-shaped multi-component composite oxide monolithic denitration catalyst, which can solve the problems that the catalyst cannot be regenerated or the regeneration is difficult, the active components are unevenly distributed, and the preparation steps are many. Conducive to denitration catalytic reduction, long service life and simple operation
- Summary
- Abstract
- Description
- Claims
- Application Information
AI Technical Summary
Problems solved by technology
Method used
Image
Examples
Embodiment 1
[0021] First remove the surface oxide of the barbed wire in dilute hydrochloric acid, ultrasonically treat it in isopropanol for 10 minutes, roll the barbed wire into a roll, dry it in vacuum, and set aside;
[0022] Put the barbed wire roll into 0.27 mol / L Ni(NO 3 ) 2 , 0.27 mol / L Mn(NO 3 ) 2 , 1.0 mol / L NH 4 In the mixed solution of Cl and 0.0015 mol / L sodium citrate, adjust the pH value to 6.5 with 10% ammonia solution. All transferred to the autoclave lined with polytetrafluoroethylene, 150 o C water heat for 12 h. The barbed wire rolls prepared by in-situ growth of multi-component composite metal hydroxide films were washed with deionized water and dried. The resulting rolls of wire mesh were placed in a muffle furnace and the temperature was programmed from room temperature to 500 o C, calcined for 5 h to obtain the final product. From figure 1 It can be seen that the composite oxide on the surface of the barbed wire obtained after calcination is a flower-like s...
Embodiment 2
[0025] First remove the surface oxide of the aluminum screen in dilute hydrochloric acid, ultrasonically treat it in isopropanol for 10 minutes, roll the aluminum screen into a roll, dry it in vacuum, and set aside;
[0026] Put the aluminum mesh roll into 1.0 mol / L Ni(NO 3 ) 2 , 2.0 mol / L Mn(NO 3 ) 2 , 6 mol / L NH 4 In the mixed solution of Cl and 0.5 mol / L sodium citrate, the pH value was adjusted to 7 with 10% ammonia solution. All transferred to a polytetrafluoro-lined autoclave, 200 o C water heat for 24 h. The aluminum wire mesh rolls prepared by in-situ growth of multi-component composite metal hydroxide films were washed with deionized water and dried. Put the obtained aluminum wire mesh roll into a muffle furnace and program the temperature from room temperature to 600 o C, calcined for 6 h to obtain the final product.
[0027] Test condition is the same as embodiment 1, at reaction temperature 270-350 o C, the measured NO conversion rate is over 80%.
Embodiment 3
[0029] First remove the surface oxide of the barbed wire in dilute hydrochloric acid, ultrasonically treat it in isopropanol for 10 minutes, roll the barbed wire into a roll, dry it in vacuum, and set aside;
[0030] Put the barbed wire roll into 3 mol / L Ni(NO 3 ) 2 , 8 mol / L Mn(NO 3 ) 2 , 10 mol / L NH 4In the mixed solution of Cl and 1 mol / L sodium citrate, the pH value was adjusted to 5.5 with 10% ammonia solution. All transferred to the autoclave lined with polytetrafluoroethylene, 150 o C water heat 8 h. The barbed wire rolls prepared by in-situ growth of multi-component composite metal hydroxide films were washed with deionized water and dried. The resulting rolls of wire mesh were placed in a muffle furnace and the temperature was programmed from room temperature to 500 o C, calcined for 12 h to obtain the final product.
[0031] Test condition is the same as embodiment 1, at reaction temperature 200-330 o C, the measured NO conversion rate is above 85%.
PUM
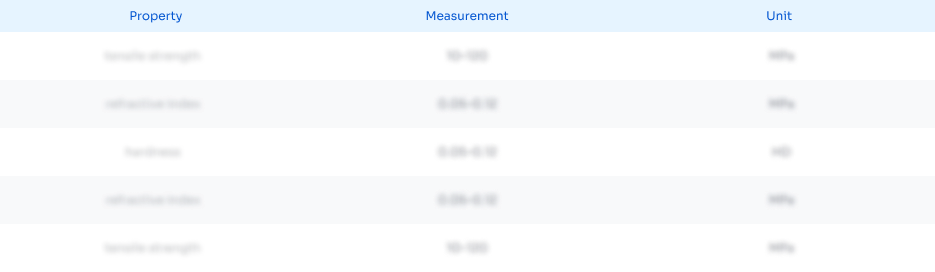
Abstract
Description
Claims
Application Information

- Generate Ideas
- Intellectual Property
- Life Sciences
- Materials
- Tech Scout
- Unparalleled Data Quality
- Higher Quality Content
- 60% Fewer Hallucinations
Browse by: Latest US Patents, China's latest patents, Technical Efficacy Thesaurus, Application Domain, Technology Topic, Popular Technical Reports.
© 2025 PatSnap. All rights reserved.Legal|Privacy policy|Modern Slavery Act Transparency Statement|Sitemap|About US| Contact US: help@patsnap.com