Coal pyrolysis system and pyrolysis method
A coal pyrolysis and coal heat technology, applied in the coal pyrolysis system and the field of pyrolysis, can solve the problems of harsh operating conditions, high equipment investment costs and high operating costs, and achieve higher productivity, lower investment costs and lower costs. Effect
- Summary
- Abstract
- Description
- Claims
- Application Information
AI Technical Summary
Problems solved by technology
Method used
Image
Examples
Embodiment 1
[0031] The coal pyrolysis method of the present embodiment comprises the following steps:
[0032] (1) After drying and preheating, the raw coal enters the coal pyrolysis reactor for pyrolysis reaction, the reaction temperature is 700°C, and the pressure is 1.5Mpa;
[0033] (2) The coal pyrolysis gas from the pyrolysis reactor enters the coal pyrolysis gas cooling and gas-liquid separation system for cooling and separation. The cooling and gas-liquid separation part adopts frozen brine at -10°C for heat exchange; After gas separation, the tar and water are separated by centrifugation, and the tar is collected; after the separated coal pyrolysis gas fan is pressurized, additional carbon dioxide is introduced into the coal pyrolysis gas catalytic activation system filled with catalysts for catalytic activation. / Al 2 o 3 Catalyst (preparation by impregnation method, Ni mass content is 11.2%, uses H before use 2 -N 2 Reduction at 750°C for 2 hours in a mixed gas), and catalyt...
Embodiment 2
[0040] Same as above-mentioned Example 1, the mixed gas of methane and carbon dioxide is supplemented during the reaction, and the volume content of methane in the mixed gas is 50%.
Embodiment 3
[0046] The experimental reaction was carried out on a small batch coal pyrolysis reaction device. The device can handle 20 kg of coal in a single batch. Coal pyrolysis gas activation in Ru / Al 2 o 3 Catalyst (preparation by impregnation method, Ru mass content is 0.59%, uses H before use 2 -N 2 Reduction in the mixed gas at 750°C for 2 hours) is carried out on a fixed bed, and carbon dioxide is supplemented by detecting the pressure of the system (when the pressure drops, the pressure of the entire system is restored by supplementing the gas). The cooling and gas-liquid separation part uses -10°C frozen brine for heat exchange. The separated mixed gas is pressurized by the fan and sent to the fixed bed reactor filled with catalyst for activation. The collected tar and water mixture is separated from oil and water by centrifugation. Pyrolysis conditions: temperature 700°C, reaction time 5 hours, pressure 1.5MPa, tar and semi-coke yields were calculated by weighing.
PUM
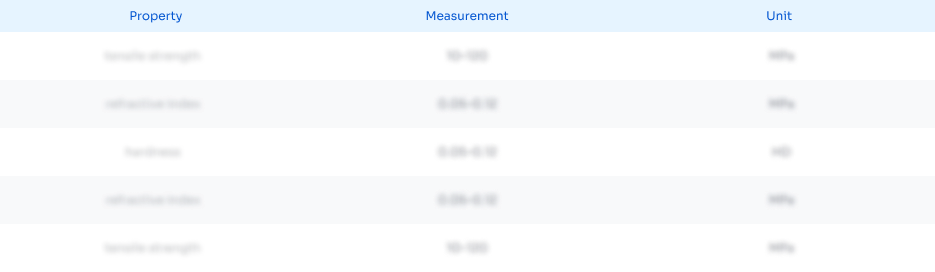
Abstract
Description
Claims
Application Information

- R&D
- Intellectual Property
- Life Sciences
- Materials
- Tech Scout
- Unparalleled Data Quality
- Higher Quality Content
- 60% Fewer Hallucinations
Browse by: Latest US Patents, China's latest patents, Technical Efficacy Thesaurus, Application Domain, Technology Topic, Popular Technical Reports.
© 2025 PatSnap. All rights reserved.Legal|Privacy policy|Modern Slavery Act Transparency Statement|Sitemap|About US| Contact US: help@patsnap.com