Chip-level bottom filling adhesive and preparation method thereof
An underfill glue and chip-level technology, which is applied in adhesives, epoxy resin glue, semiconductor/solid-state device components, etc., can solve the problem of unsuitable high-density packaging of memory chips, low radioactivity, and curing shrinkage. Advanced problems, to achieve the effect of low curing shrinkage, small particle diameter and low radioactivity
- Summary
- Abstract
- Description
- Claims
- Application Information
AI Technical Summary
Problems solved by technology
Method used
Examples
Embodiment 1
[0034] Accurately weigh the following raw materials, alicyclic epoxy resin 5g, polycyclic aromatic epoxy resin 10g, rubber modified resin 1g, BYK-9076 0.1g, BYK-A530 0.1g, β-(3,4- Put 5.3g of epoxycyclohexyl)ethyltrimethoxysilane and 0.5g of carbon black into the reaction kettle and stir for 0.5 to 1 hour to form a homogeneous solution; then weigh 70g of low-radioactive silicon micropowder with an average diameter of Stir in the reaction kettle for 2-4 hours; then weigh 3g of modified amine curing agent, at this time, the temperature is controlled at 20-30°C, put the curing agent into the reaction kettle, stir for 1-2 hours, and mix well; Finally, weigh 5g of neopentyl glycol diglycidyl ether, put it into the reaction kettle, vacuum degree -0.098~-0.095MPa, rotate speed 300~600 rpm, stir for 1~2 hours, form a uniform solution, and obtain the product.
Embodiment 2
[0036] Accurately weigh the following raw materials, polycyclic aromatic epoxy resin 10g, bisphenol A epoxy resin 10g, rubber modified resin 3g, BYK-W9010 0.2g, PC-1344 0.4g, γ-glycidyloxy Put 10 g of propyltrimethoxysilane and 0.4 carbon black into the reactor and stir for 0.5 to 1 hour to form a homogeneous solution, then weigh 50 g of low-radioactive silicon micropowder with an average diameter of 15 microns, put it into the reactor and stir for 2 to 1 hour. 4 hours; then weigh 7g of modified amine curing agent, at this time the temperature is controlled at 20-30°C, put this curing agent into the reaction kettle, stir for 1-2 hours, and mix well; finally weigh 4-tert-butyl Put 9g of phenyl glycidyl ether into the reaction kettle, vacuum degree -0.098~-0.095MPa, rotation speed 300~600 rpm, stir for 1~2 hours, form a homogeneous solution, and obtain the product.
Embodiment 3
[0038] Accurately weigh the following raw materials, alicyclic epoxy resin 15g, phenolic epoxy resin 10g, silicone modified resin 2.5g, BYK-W985 0.15g, PC-1244 0.1g, γ-aminopropyl triethyl Put 5.8g of oxysilane and 0.45 of carbon black into the reactor and stir for 0.5-1 hour to form a homogeneous solution, then weigh 48g of low-radioactive silicon micropowder with an average diameter of 10 microns, put it into the reactor and stir for 2-4 hours ; Then weigh 10g of acid anhydride curing agent, at this time, the temperature is controlled at 20-30°C, put the curing agent into the reaction kettle, stir for 1-2 hours, and mix well; finally weigh the dodecyl to tetradecyl shrink Put 8g of glycerol ether into the reaction kettle, the vacuum degree is -0.098~-0.095MPa, the rotation speed is 300~600 rpm, and it is stirred for 1~2 hours to form a homogeneous solution to obtain the product.
PUM
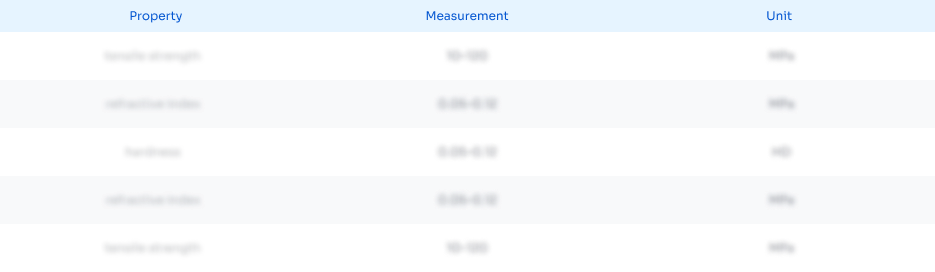
Abstract
Description
Claims
Application Information

- R&D Engineer
- R&D Manager
- IP Professional
- Industry Leading Data Capabilities
- Powerful AI technology
- Patent DNA Extraction
Browse by: Latest US Patents, China's latest patents, Technical Efficacy Thesaurus, Application Domain, Technology Topic, Popular Technical Reports.
© 2024 PatSnap. All rights reserved.Legal|Privacy policy|Modern Slavery Act Transparency Statement|Sitemap|About US| Contact US: help@patsnap.com