Single-iron notch blast furnace main channel self-flow repairing material
A self-flow repairing material and blast furnace technology, which is applied in the field of blast furnace ironmaking refractories, can solve the problems of insufficient explosion-proof performance and self-flow penetration performance, inability to repair small cracks, unsuitable and other problems, so as to improve the overall service life and utilization rate. The effect of self-flow performance, good high permeability
- Summary
- Abstract
- Description
- Claims
- Application Information
AI Technical Summary
Problems solved by technology
Method used
Examples
Embodiment 1
[0016] Self-flowing repair material for the main ditch of a single iron hole blast furnace, brown corundum or dense corundum: 46 parts, silicon carbide superfine powder: 20 parts, white corundum: 13 parts, α-Al 2 o 3 : 5 parts, silica powder: 2 parts, paraffin wax: 1.6 parts, spherical pitch: 5 parts, metal silicon: 3 parts, ethylene glycol: 1 part, chromium oxide: 0.2 parts, boron nitride: 0.5 parts, zirconia: 0.2 part, composite additive: 2 parts, composite explosion-proof agent: 0.5 part, present embodiment is the best embodiment. The composite additive includes the following components and the mass percentage of each component is: water reducer: 20%-30%, dispersant: 10%-25%, antioxidant: 45%-55%, hardener: 20%- 25%. The water reducer is polycarboxylate water reducer, the dispersant is sodium polyacrylate, the antioxidant is boron carbide, and the hardener is tetraethylenepentamine. The composite anti-explosion agent includes the following components and the mass percent...
Embodiment 2
[0019] The mass ratio of each component is: brown corundum or dense corundum: 49 parts, silicon carbide superfine powder: 18 parts, white corundum: 12 parts, α-Al 2 o 3 : 6 parts, silica powder: 1.2 parts, paraffin wax: 1 part, spherical pitch: 5.2 parts, metal silicon: 3.5 parts, ethylene glycol: 1.2 parts, chromium oxide: 0.3 parts, boron nitride: 0.6 parts, zirconia: 0.3 parts, composite additives: 1.5 parts, composite explosion-proof agent: 0.3 parts, the cost of this formula is lower.
Embodiment 3
[0021] The mass ratio of each component is: brown corundum or dense corundum: 42 parts, silicon carbide superfine powder: 23 parts, white corundum: 15 parts, α-Al 2 o 3 : 5 parts, silica powder: 2.3 parts, paraffin wax: 1.3 parts, spherical pitch: 4.9 parts, metal silicon: 3.5 parts, ethylene glycol: 1.3 parts, chromium oxide: 0.25 parts, boron nitride: 0.7 parts, zirconia: 0.26 parts, composite additive: 2.1 parts, composite explosion-proof agent: 0.4 parts, the effect of this formula is better.
PUM
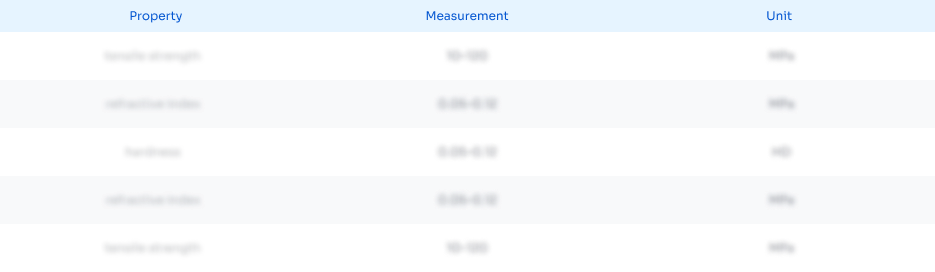
Abstract
Description
Claims
Application Information

- Generate Ideas
- Intellectual Property
- Life Sciences
- Materials
- Tech Scout
- Unparalleled Data Quality
- Higher Quality Content
- 60% Fewer Hallucinations
Browse by: Latest US Patents, China's latest patents, Technical Efficacy Thesaurus, Application Domain, Technology Topic, Popular Technical Reports.
© 2025 PatSnap. All rights reserved.Legal|Privacy policy|Modern Slavery Act Transparency Statement|Sitemap|About US| Contact US: help@patsnap.com