TIG (tungsten inert gas) welding method for auxiliary mechanical vibration droplet transfer and TIG welding device for same
A technology of mechanical vibration and droplet transfer, applied in welding equipment, welding accessories, arc welding equipment, etc., can solve the problems of uneven structure of welding seam, affecting the stability of arc, large width of heat-affected zone, etc., and achieve uniform structure. The effect of good performance, improved efficiency, and accelerated droplet transfer frequency
- Summary
- Abstract
- Description
- Claims
- Application Information
AI Technical Summary
Problems solved by technology
Method used
Image
Examples
Embodiment 1
[0022] Example 1: Combining figure 1 , the present invention a kind of TIG welding device of mechanical vibration auxiliary droplet transfer, it is by TIG power supply (1), frame (2), wire feeder (3), conduit (4), auxiliary mechanical vibration device (5) , wire feeder (7) and welding wire (8), the wire feeder (3) is connected to the conduit (4), the conduit (4) is connected to the wire feeder (7), and the wire feeder (7) is connected to the frame (2 ) are firmly connected, and the auxiliary mechanical vibration device (5) is fixed on the frame (2).
[0023] Described auxiliary mechanical vibrating device (5) comprises fuselage (5-1), buffer spring (5-2), vibrating bar (5-3) and contact (5-4), is built-in by fuselage drive motor and The transmission device drives the vibrating rod (5-3) to reciprocate up and down, the vibrating rod (5-3) and the contact (5-4) are threaded, and the vibrating rod (5-3) and the contact (5-4) A buffer spring (5-2) is sleeved between, and the buf...
Embodiment 2
[0029] Example 2: Combining figure 1 , figure 2 , the present invention is a mechanical vibration-assisted droplet transfer TIG welding method, the welding wire material is a material with high hardness and good rigidity, such as stainless steel. The welding wire (8) is output by the wire feeder (3), enters the arc (9) area after passing through the conduit (4) and the wire feed nozzle (7), and processes a process groove of an appropriate size on the wire feed nozzle (7). Both the vibrating effect and the stability of the wire feed nozzle (7) need to be combined, and the size of the slot is determined by the front end of the contact (5-4), so as to fully transmit the vibration effect.
[0030]The principle of realizing the cold metal transition is that the auxiliary mechanical vibration device (5) causes the vibration rod (5-3) to generate mechanical vibration, and the contact (5-4) and the vibration rod (5-3) reciprocate up and down, and the vibration is caused by the conta...
Embodiment 3
[0031] Embodiment 3: The welding wire is a material with low hardness and poor rigidity, such as tin. At this time, the contact (5-4) is in direct contact with the outer wall of the wire feeding nozzle (7), avoiding the deformation of the welding wire (8) caused by mechanical vibration, and destroying the continuity of the automatic wire feeding process. The vibration is transmitted from the contact (5-4) to the The wire feed nozzle (7) is then transmitted to the welding wire (8), and an additional mechanical force is generated at the end of the welding wire (8). Other steps, connection methods and principles are the same as those in Embodiment 2.
[0032] By adjusting the rotational speed of the built-in driving motor of the auxiliary mechanical vibration device (5), the mechanical vibration of the vibration rod (5-3) within the frequency range of 2 to 30 times per second can be realized, and a higher vibration frequency can be selected for welding wires with larger diameters ...
PUM
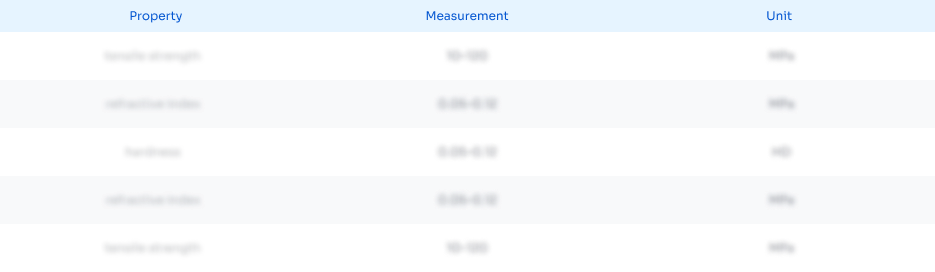
Abstract
Description
Claims
Application Information

- Generate Ideas
- Intellectual Property
- Life Sciences
- Materials
- Tech Scout
- Unparalleled Data Quality
- Higher Quality Content
- 60% Fewer Hallucinations
Browse by: Latest US Patents, China's latest patents, Technical Efficacy Thesaurus, Application Domain, Technology Topic, Popular Technical Reports.
© 2025 PatSnap. All rights reserved.Legal|Privacy policy|Modern Slavery Act Transparency Statement|Sitemap|About US| Contact US: help@patsnap.com