Manufacturing method of highly-conductive and heat-resisting electrode cross beam component
A high-conductivity, heat-resistant technology, applied in the field of industrial manufacturing, can solve the problems of casting technology development that have not been reported, and achieve the effect of rapid prototyping, low cost and improved conductivity
- Summary
- Abstract
- Description
- Claims
- Application Information
AI Technical Summary
Problems solved by technology
Method used
Examples
Embodiment 1
[0030] A method for casting a high-conductivity heat-resistant electrode beam component, comprising the following steps:
[0031] (1) Select alloy materials;
[0032] (2) Manufacture metal molds that meet the size of the parts;
[0033] (3) Melting and molding of cast alloy materials;
[0034] (4), heat treatment is carried out to the casting of cast molding, it is characterized in that:
[0035] The composition of the alloy material used includes Al, Mg, Si, Zr, Ce, B elements; the mass percentage of each composition is:
[0036] Mg: 0.5~1.0%, Si: 0.4~0.8%, Zr: 0.6~0.8%, Ce: 0.05~0.1%, B: 0.03~0.06%; the balance is Al and unavoidable impurities;
[0037] The mass percentages of impurity elements contained in the alloy material are: Fe≤0.2%, Cu≤0.05%, Mn≤0.02%, Cr≤0.02%, Zn≤0.05%, Ti≤0.05%.
[0038] The melting and forming steps of casting alloy materials are as follows:
[0039] 1) First add industrial pure Al after the crucible is preheated;
[0040] 2) Heat the melt t...
Embodiment 2
[0047] A method for casting a high-conductivity heat-resistant electrode beam component, comprising the following steps:
[0048] (1) Select alloy material;
[0049] (2) Manufacture metal molds that meet the size of the parts;
[0050] (3) Melting and molding of cast alloy materials;
[0051] (4), heat treatment is carried out to the casting of cast molding, it is characterized in that:
[0052] The composition of the alloy material used includes Al, Mg, Si, Zr, Ce, B elements; the mass percentage of each composition is:
[0053] Mg: 0.5~1.0%, Si: 0.4~0.8%, Zr: 0.6~0.8%, Ce: 0.05~0.1%, B: 0.03~0.06%; the balance is Al and unavoidable impurities;
[0054] The mass percentages of impurity elements contained in the alloy material are: Fe≤0.2%, Cu≤0.05%, Mn≤0.02%, Cr≤0.02%, Zn≤0.05%, Ti≤0.05%.
[0055] The melting and forming steps of casting alloy materials are as follows:
[0056] 1) First add industrial pure Al after the crucible is preheated;
[0057] 2) Heat up the melt t...
Embodiment 3
[0064] 1. A method for casting a high-conductivity heat-resistant electrode beam component, comprising the following steps:
[0065] (1) Select alloy materials;
[0066] (2) Manufacture metal molds that meet the size of the parts;
[0067] (3) Melting and molding of cast alloy materials;
[0068] (4), heat treatment is carried out to the casting of cast molding, it is characterized in that:
[0069] The composition of the alloy material used includes Al, Mg, Si, Zr, Ce, B elements; the mass percentage of each composition is:
[0070] Mg: 0.5~1.0%, Si: 0.4~0.8%, Zr: 0.6~0.8%, Ce: 0.05~0.1%, B: 0.03~0.06%; the balance is Al and unavoidable impurities;
[0071] The mass percentages of impurity elements contained in the alloy material are: Fe≤0.2%, Cu≤0.05%, Mn≤0.02%, Cr≤0.02%, Zn≤0.05%, Ti≤0.05%.
[0072] The melting and forming steps of casting alloy materials are as follows:
[0073] 1) First add industrial pure Al after the crucible is preheated;
[0074] 2) Raise the te...
PUM
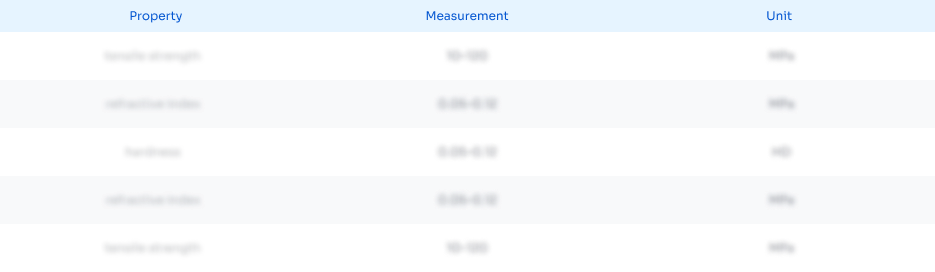
Abstract
Description
Claims
Application Information

- R&D Engineer
- R&D Manager
- IP Professional
- Industry Leading Data Capabilities
- Powerful AI technology
- Patent DNA Extraction
Browse by: Latest US Patents, China's latest patents, Technical Efficacy Thesaurus, Application Domain, Technology Topic, Popular Technical Reports.
© 2024 PatSnap. All rights reserved.Legal|Privacy policy|Modern Slavery Act Transparency Statement|Sitemap|About US| Contact US: help@patsnap.com