Non-contact annular magnetoelectric rotary encoder
A rotary encoder and annular technology, applied in the field of sensors, can solve the problems of complex mechanical structure, cumbersome installation and adjustment process, and high precision requirements, and achieve the effect of simplifying the mechanical structure, simplifying the mechanical structure, and maintaining high precision.
- Summary
- Abstract
- Description
- Claims
- Application Information
AI Technical Summary
Problems solved by technology
Method used
Image
Examples
Embodiment Construction
[0019] attached by figure 1 , 2 As shown: the encoder is composed of two parts: the ring encoder body I and the acquisition head II with a gap between the ring encoder body I and the corresponding encoder body I. The encoder body I includes a bearing ring 1. The magnetic ring 2 attached to the upper edge of the bearing body 1, and the protective cover 3 arranged outside the ring bearing ring body 1 and the magnetic ring 2 to protect the magnetic ring 2.
[0020] attached by image 3 As shown: the magnetic coil 2 is specially magnetized according to different pulse requirements, and its N and S polarities are alternately arranged along the circumferential surface of the magnetic coil 2, and the number is an even number.
[0021] attached by Figure 4 As shown: the collection head II includes an upper cover 4, a lower cover 5 with a brush head 8 on the end face, a circuit board 6 arranged inside the upper cover 4 and the lower cover 5, and a magnetic induction chip 7 arranged...
PUM
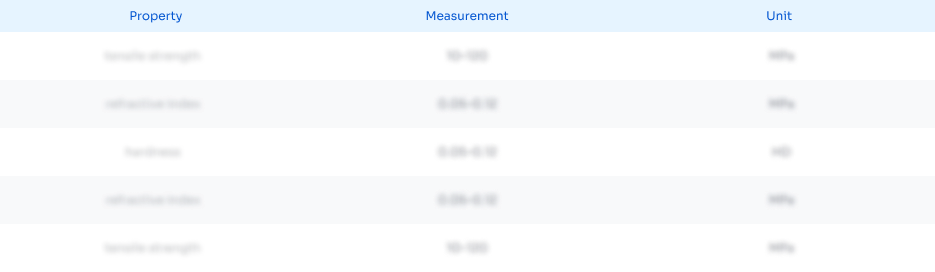
Abstract
Description
Claims
Application Information

- R&D
- Intellectual Property
- Life Sciences
- Materials
- Tech Scout
- Unparalleled Data Quality
- Higher Quality Content
- 60% Fewer Hallucinations
Browse by: Latest US Patents, China's latest patents, Technical Efficacy Thesaurus, Application Domain, Technology Topic, Popular Technical Reports.
© 2025 PatSnap. All rights reserved.Legal|Privacy policy|Modern Slavery Act Transparency Statement|Sitemap|About US| Contact US: help@patsnap.com