Zinc-aluminum-magnesium-rare earth multi-element alloy material and preparation method thereof
A multi-element alloy, zinc-aluminum-magnesium technology, applied in metal material coating process, coating, melt spraying and other directions, can solve problems such as instability
- Summary
- Abstract
- Description
- Claims
- Application Information
AI Technical Summary
Problems solved by technology
Method used
Image
Examples
Embodiment Construction
[0043] 1. Preparation of zinc-aluminum-magnesium rare earth multi-element alloy materials
[0044] Step 1: First, add an aluminum ingot with a purity of 99.5% (the weight percentage of Al: 90%) into the graphite clay crucible, heat up the furnace until the aluminum ingot is melted, raise the furnace temperature to 830°C, and crush metal La and Ce Blocks (5.0% by weight of La and 5.0% by weight of Ce) were pressed into molten aluminum in batches. After the metals La and Ce are completely melted, they are fully stirred and cast to form the master alloy ALRe10, and the casting temperature of the alloy is 1250°C.
[0045] Step 2: Put zinc ingots with a purity of 99.995% and aluminum ingots with a purity of 99.5% into a vacuum induction melting furnace for melting, use 0.1-0.5wt% zinc chloride refining agent and 0.05-0.07wt% modificant (chlorine ammonium chloride) for treatment, the main component of the modifier is RE-45, and then 5.0% ALRe10 aluminum-based rare earth master allo...
PUM
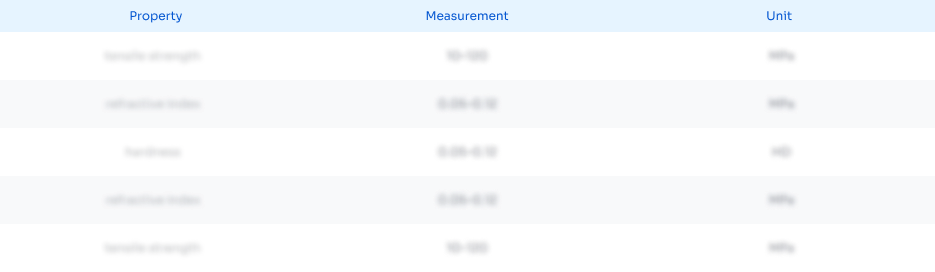
Abstract
Description
Claims
Application Information

- Generate Ideas
- Intellectual Property
- Life Sciences
- Materials
- Tech Scout
- Unparalleled Data Quality
- Higher Quality Content
- 60% Fewer Hallucinations
Browse by: Latest US Patents, China's latest patents, Technical Efficacy Thesaurus, Application Domain, Technology Topic, Popular Technical Reports.
© 2025 PatSnap. All rights reserved.Legal|Privacy policy|Modern Slavery Act Transparency Statement|Sitemap|About US| Contact US: help@patsnap.com