Grid mould release agent
A release agent and grid technology, applied in coating, casting molding equipment, mold and other directions, can solve the problems of unstable product quality, poor release agent molding, low production efficiency, etc., to achieve smooth exhaust, easy The effect of demoulding and prolonging the service life
- Summary
- Abstract
- Description
- Claims
- Application Information
AI Technical Summary
Problems solved by technology
Method used
Image
Examples
Embodiment 1
[0029] Embodiment 1: A grid release agent, the mass percentage of each component is as follows: water 95.0%, polytetrafluoroethylene: 0.3%, cork powder 4.0%, aluminum dihydrogen phosphate 0.2%, adhesive 0.15%, stable 0.35% agent, mixed and prepared according to the above ratio to form an emulsion, heated, stirred, and cooled to form a release agent. It has the advantages of easy spraying, good adhesion, high temperature resistance, small surface tension, high pressure resistance, and smooth exhaust. It is very suitable for The high-temperature gravity-cast lead-calcium alloy grid can effectively reduce the pores and cracks of the grid, and at the same time reduce the number of injection molds per unit time, improve production efficiency and improve product quality.
Embodiment 2
[0030] Embodiment 2: A grid release agent, the mass percentage of each component is as follows: water 97.0%, polytetrafluoroethylene: 0.1%, cork powder 2.4%, aluminum dihydrogen phosphate 0.18%, adhesive 0.12%, stable 0.2% agent, according to the above ratio, mixed and prepared into an emulsion, heated, stirred, and cooled to form a release agent, which has the advantages of easy spraying, good adhesion, high temperature resistance, small surface tension, high pressure resistance, and smooth exhaust, etc., very suitable for The high-temperature gravity-cast lead-calcium alloy grid can effectively reduce the pores and cracks of the grid, and at the same time reduce the number of injection molds per unit time, improve production efficiency and improve product quality.
Embodiment 3
[0031] Embodiment 3: A grid release agent, the mass percentage of each component is as follows: water 96.0%, polytetrafluoroethylene: 0.2%, cork powder 3.2%, aluminum dihydrogen phosphate 0.17%, adhesive 0.13%, stable 0.3% agent, according to the above ratio, mixed and prepared into an emulsion, heated, stirred, and cooled to form a release agent, which has the advantages of easy spraying, good adhesion, high temperature resistance, small surface tension, high pressure resistance, and smooth exhaust, and is very suitable for The high-temperature gravity-cast lead-calcium alloy grid can effectively reduce the pores and cracks of the grid, and at the same time reduce the number of injection molds per unit time, improve production efficiency and improve product quality.
[0032] The production process of the above-mentioned release agent: heat water to boiling, add bone glue and polyvinyl alcohol to melt completely, add aluminum dihydrogen phosphate and cork powder and boil for 10...
PUM
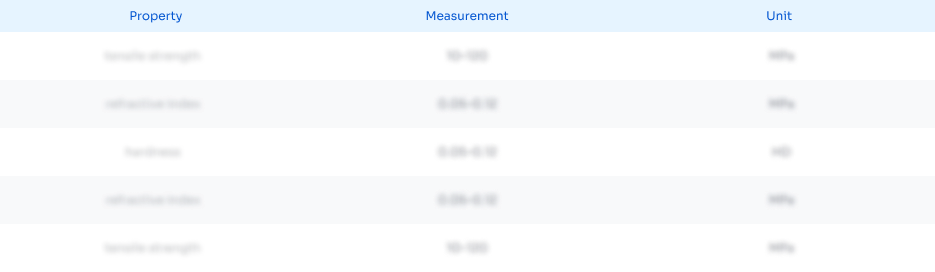
Abstract
Description
Claims
Application Information

- Generate Ideas
- Intellectual Property
- Life Sciences
- Materials
- Tech Scout
- Unparalleled Data Quality
- Higher Quality Content
- 60% Fewer Hallucinations
Browse by: Latest US Patents, China's latest patents, Technical Efficacy Thesaurus, Application Domain, Technology Topic, Popular Technical Reports.
© 2025 PatSnap. All rights reserved.Legal|Privacy policy|Modern Slavery Act Transparency Statement|Sitemap|About US| Contact US: help@patsnap.com