High-property automobile plastic bracket and manufacturing method thereof
A technology for plastic brackets and manufacturing methods, applied in the direction of coating, etc., can solve problems such as whitening, poor toughness, and low strength, and achieve the effects of improving production efficiency, stable product quality, and reducing production costs
- Summary
- Abstract
- Description
- Claims
- Application Information
AI Technical Summary
Problems solved by technology
Method used
Image
Examples
Embodiment 1
[0018] Embodiment 1: High-performance automobile plastic bracket, its composition raw material comprises composition A and composition B, described composition A: 45 parts of polypropylene, 45 parts of polypropylene+30%GF, 10 parts of polyvinyl chloride resin and 3 parts of titanium dioxide; Composition B: 40 parts of glass fiber, 10 parts of nitrile modified phenolic resin, 3 parts of magnesium hydroxide, 10 parts of phenolic resin, 5 parts of titanium dioxide, 5 parts of high wear-resistant carbon black, 5 parts of tetrafluoroethylene parts, 5 parts of silane coupling agent and 3 parts of isoglutaric acid.
[0019] A method for manufacturing a high-performance automotive plastic bracket, comprising the following steps:
[0020] (1) Weigh each raw material according to the weight part of composition A raw material, carry out drying treatment, drying temperature is 80-100 ℃, drying time is 1-2 hour, mix evenly, put into dryer, at 140-160 ℃ Dry for 24-28 hours;
[0021] (2) W...
Embodiment 2
[0028] Embodiment 2: high-performance automobile plastic bracket, its composition raw material comprises composition A and composition B, described composition A: 55 parts of polypropylene, 55 parts of polypropylene+30%GF, 20 parts of polyvinyl chloride resin and 8 parts of titanium dioxide; Composition B: 50 parts of glass fiber, 20 parts of nitrile modified phenolic resin, 8 parts of magnesium hydroxide, 15 parts of phenolic resin, 10 parts of titanium dioxide, 10 parts of high wear-resistant carbon black, 15 parts of tetrafluoroethylene parts, 10 parts of silane coupling agent and 8 parts of isoglutaric acid.
[0029] A method for manufacturing a high-performance automotive plastic bracket, comprising the following steps:
[0030] (1) Weigh each raw material according to the weight part of composition A raw material, carry out drying treatment, drying temperature is 80-100 ℃, drying time is 1-2 hour, mix evenly, put into dryer, at 140-160 ℃ Dry for 24-28 hours;
[0031] (...
PUM
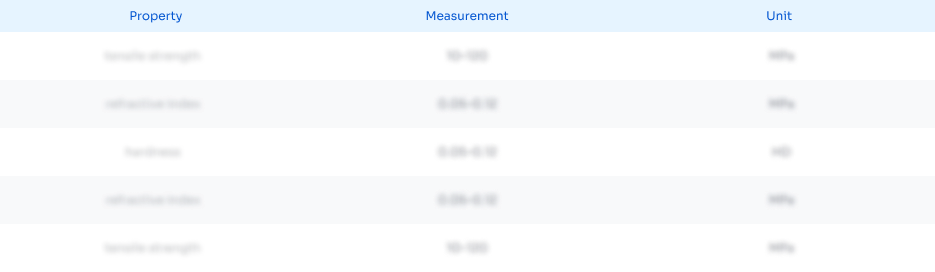
Abstract
Description
Claims
Application Information

- R&D
- Intellectual Property
- Life Sciences
- Materials
- Tech Scout
- Unparalleled Data Quality
- Higher Quality Content
- 60% Fewer Hallucinations
Browse by: Latest US Patents, China's latest patents, Technical Efficacy Thesaurus, Application Domain, Technology Topic, Popular Technical Reports.
© 2025 PatSnap. All rights reserved.Legal|Privacy policy|Modern Slavery Act Transparency Statement|Sitemap|About US| Contact US: help@patsnap.com