Method for treating wastewater produced in process for directly liquefying coal
A technology of direct coal liquefaction and treatment method, which is applied in the field of treatment of direct coal liquefaction wastewater, can solve the problems of low treatment efficiency and complicated treatment process of direct coal liquefaction wastewater, and achieves the effect of improving treatment efficiency and simple process
- Summary
- Abstract
- Description
- Claims
- Application Information
AI Technical Summary
Problems solved by technology
Method used
Image
Examples
Embodiment 1
[0029] Catalyst preparation: take TiSO 4 And ZrSO 4 40 grams each, dissolved in 1000ml distilled water to make a solution, add ammonia water to the solution with stirring until the pH value is 10, and then filter and repeatedly rinse the filter cake with deionized water to SO in the rinse solution 4 2- When the concentration is less than 0.1ppm, the obtained filter cake is extruded and formed, then the temperature is programmed (10℃ / min) to 120℃, kept for 10 hours, and then heated to 700℃ at the same programmed temperature rate, and it is made after high temperature roasting for 10 hours. TiO 2 -ZrO 2 The composite oxide carrier is prepared by using the soluble salt of the corresponding active components (Cu, Mn, La, Co) to make an aqueous solution, which is loaded on the prepared composite carrier by an equal volume impregnation method, and each active component is loaded The amount is Cu 6%, Mn 2%, La 2%, Co 1%. Subsequently, the temperature was programmed (10°C / min) to 120°C ...
Embodiment 2
[0033] Preparation of catalyst: Take 60 grams of TiSO 4 And 20 grams of ZrSO 4 , Dissolved in 1000ml of distilled water to make a solution, add ammonia water to the solution with stirring until the pH value is 10, then filter and repeatedly rinse the filter cake with deionized water to SO in the rinse solution 4 2- When the concentration is less than 0.1ppm, the obtained filter cake is extruded and formed, then the temperature is programmed (10℃ / min) to 120℃, kept for 10 hours, and then heated to 700℃ at the same programmed temperature rate, and it is made after high temperature roasting for 10 hours. TiO 2 -ZrO 2 The composite oxide carrier is prepared by using the soluble salt of the corresponding active components (Cu, Mn, La, Co) to make an aqueous solution, which is loaded on the prepared composite carrier by an equal volume impregnation method, and each active component is loaded The amount is Cu 6%, Mn 2%, La 2%, Co 1%. Subsequently, the temperature was programmed (10°C / m...
Embodiment 3
[0037] Preparation of catalyst: Take 60 grams of TiSO 4 And 20 grams of ZrSO 4 , Dissolved in 1000ml of distilled water to make a solution, add ammonia water to the solution with stirring until the pH value is 10, then filter and repeatedly rinse the filter cake with deionized water to SO in the rinse solution 4 2- When the concentration is less than 0.1ppm, the obtained filter cake is extruded, and then the temperature is programmed (10°C / min) to 120°C, kept for 10 hours, and then the temperature is raised to 800°C at the same programmed temperature rate, and the product is calcined at high temperature for 10 hours. TiO 2 -ZrO 2 The composite oxide carrier is prepared by using the soluble salt of the corresponding active components (Cu, Mn, La, Ni, Fe) to make an aqueous solution, and load it on the prepared composite carrier by an isometric impregnation method. The partial load is Cu 5%, Mn 3%, La 2%, Ni 2%, Fe 1%. Subsequently, the temperature was programmed (10°C / min) to 120...
PUM
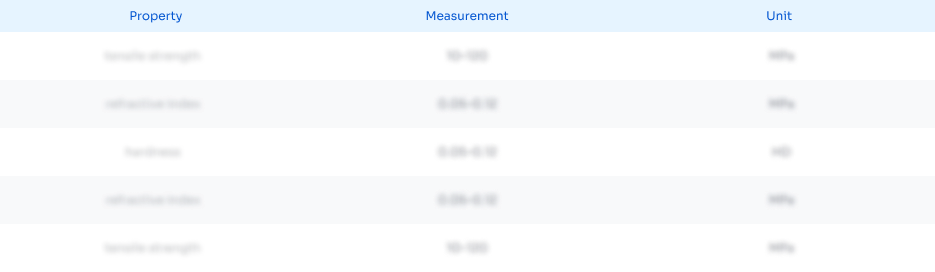
Abstract
Description
Claims
Application Information

- R&D
- Intellectual Property
- Life Sciences
- Materials
- Tech Scout
- Unparalleled Data Quality
- Higher Quality Content
- 60% Fewer Hallucinations
Browse by: Latest US Patents, China's latest patents, Technical Efficacy Thesaurus, Application Domain, Technology Topic, Popular Technical Reports.
© 2025 PatSnap. All rights reserved.Legal|Privacy policy|Modern Slavery Act Transparency Statement|Sitemap|About US| Contact US: help@patsnap.com