High-speed spindle with tapered hole capable of being automatically locked
An automatic locking, high-speed spindle technology, used in metal processing equipment and other directions, can solve the problems of increased wear of the shank taper, excessive bearing preload, increased flexibility of the shank taper, etc., and achieve high radial positioning. Accuracy, increase the stiffness of the connection, and increase the effect of the limit speed
- Summary
- Abstract
- Description
- Claims
- Application Information
AI Technical Summary
Problems solved by technology
Method used
Image
Examples
Embodiment 1
[0014] exist figure 1 In the schematic diagram of the high-speed spindle structure with tapered holes that can be automatically locked, the inner hole of the shaft end of the spindle 1 is fixedly connected with the expansion wall 2 with a tapered hole through an interference fit. The taper of the expansion wall taper hole is 1:10. Two annular oil chambers 3 are opened on the outer surface of the expansion wall, and the oil chambers are filled with liquid medium (such as hydraulic oil). There are two radial hydraulic cylinder installation blind holes on the outer surface of the main shaft, and the two blind holes are symmetrically distributed with respect to the main shaft axis. Two axial oil passages 4 are opened on the end surface of the main shaft in the axial direction, respectively communicating with the above two symmetrical blind holes, and the openings of the oil passages on the end surface of the main shaft are sealed. The main shaft is provided with a radial oil pass...
Embodiment 2
[0016] Its structure is the same as embodiment 1, and the piston is a stepped cylinder, such as Figure 4 shown.
[0017] The oil passages on each side of the main shaft are connected to an oil cavity through their respective radial oil passages, and the oil passages on both sides of the main shaft are not connected.
PUM
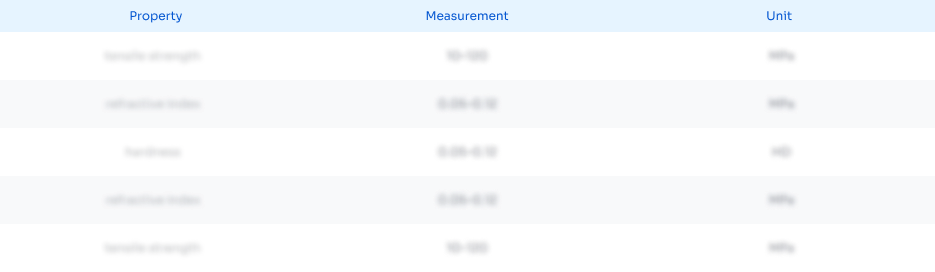
Abstract
Description
Claims
Application Information

- R&D Engineer
- R&D Manager
- IP Professional
- Industry Leading Data Capabilities
- Powerful AI technology
- Patent DNA Extraction
Browse by: Latest US Patents, China's latest patents, Technical Efficacy Thesaurus, Application Domain, Technology Topic, Popular Technical Reports.
© 2024 PatSnap. All rights reserved.Legal|Privacy policy|Modern Slavery Act Transparency Statement|Sitemap|About US| Contact US: help@patsnap.com