Permanent magnet low frequency single-degree-of-freedom vibration isolation mechanism based on negative stiffness theory
A technology with a degree of freedom and negative stiffness, applied in the direction of magnetic springs, mechanical equipment, spring/shock absorber functional characteristics, etc., can solve problems such as small load-bearing capacity, and achieve high load-bearing capacity, low cost, and good vibration isolation performance.
- Summary
- Abstract
- Description
- Claims
- Application Information
AI Technical Summary
Problems solved by technology
Method used
Image
Examples
Embodiment Construction
[0016] figure 1 2 is a structural schematic diagram of the ring-shaped permanent magnet low-frequency single-degree-of-freedom vibration isolation mechanism based on the principle of negative stiffness provided by the present invention. The ring-shaped permanent magnet low-frequency single-degree-of-freedom vibration isolation mechanism includes an inner ring permanent magnet 10 and an outer ring permanent magnet 5 , Upper rubber sheet 1, lower rubber sheet 6, inner annular permanent magnet fixed mandrel 2, upper rubber sheet upper pressure ring 3, upper rubber sheet outer pressure ring 4, lower rubber sheet inner pressure sheet 7, lower rubber sheet outer pressure ring 8 And the outer annular permanent magnet fixing sleeve 9; the inner annular permanent magnet 10 is axially magnetized, the outer annular permanent magnet 5 is radially magnetized, and the inner annular permanent magnet and the outer annular permanent magnet are arranged concentrically; the inner annular permanen...
PUM
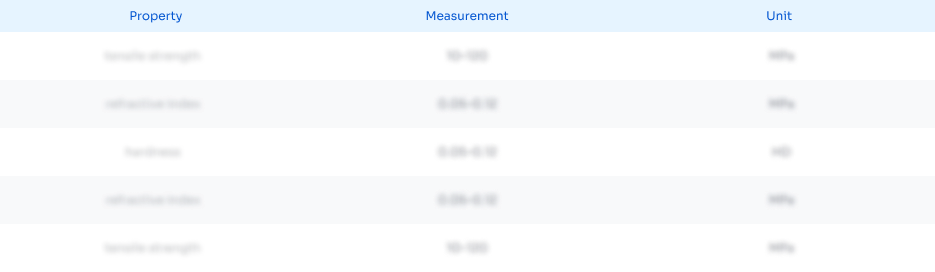
Abstract
Description
Claims
Application Information

- R&D Engineer
- R&D Manager
- IP Professional
- Industry Leading Data Capabilities
- Powerful AI technology
- Patent DNA Extraction
Browse by: Latest US Patents, China's latest patents, Technical Efficacy Thesaurus, Application Domain, Technology Topic, Popular Technical Reports.
© 2024 PatSnap. All rights reserved.Legal|Privacy policy|Modern Slavery Act Transparency Statement|Sitemap|About US| Contact US: help@patsnap.com