Method for preparing biodiesel by mixing waste edible oil with mineral diesel oil and hydrogenization
A technology for kitchen waste oil and biodiesel, which is applied in the preparation of liquid hydrocarbon mixtures, biofuels, biomaterials, etc., can solve the problems of decreased catalyst activity, poor storage stability, and large influence on hydrogenation catalyst activity, and achieves Highly active effect
- Summary
- Abstract
- Description
- Claims
- Application Information
AI Technical Summary
Problems solved by technology
Method used
Image
Examples
Embodiment 1
[0041] Pretreatment of kitchen waste oils and fats: the method is to mix oil and water at a ratio of 1:6 and heat to 75°C to elute the salt. After standing and layering to remove the water phase, heat to 120°C and keep for 30 minutes to remove excess water. , filtered through a filter with a precision of 0.1 mm, and then put into a vacuum drying tower, at 120° C. and 40 kPa (absolute pressure), the material is dried under reduced pressure for further dehydration. The pretreated kitchen waste oil is mixed with dimethyl disulfide at 0.05m% of the total feed, and then mixed with hydrogen at a volume ratio of hydrogen to oil of 1000:1. hydrogenation reactor. At a hydrogen partial pressure of 2.4MPa, the average reaction temperature is 280°C, and the total space velocity is 0.75h -1 (where the space velocity of the protective catalyst is 1.0h -1 , treatment catalyst space velocity 3.0h -1 ) under the conditions of hydrogenation of iron, calcium, sodium and other metal ions and d...
Embodiment 2
[0043] Catalyzed diesel oil and oil produced from kitchen waste oil after pretreatment and hydrogenation in the first stage enter the second stage hydrogenation reaction system at a ratio of 80:20. The conditions for the second stage hydrogenation are: hydrogen partial pressure 12.0MPa, average reaction temperature 370℃, total space velocity 1.0h -1 , The volume ratio of hydrogen to oil is 1200:1. Other methods and conditions are the same as in Example 1. 12% naphtha fraction, 28% kerosene fraction, 33% light diesel fraction and 18% heavier diesel fraction were obtained. The main properties of the product are shown in Table 3.
[0044] Table 1 Main properties of raw materials of mineral diesel oil and catering waste oil
[0045]
[0046] Table 2 Example 1 product main properties
[0047] naphtha fraction
Kerosene fraction
Light diesel products
heavier diesel products
Yield, %(m)
15
25
30
22
Density at 20°C, kg...
PUM
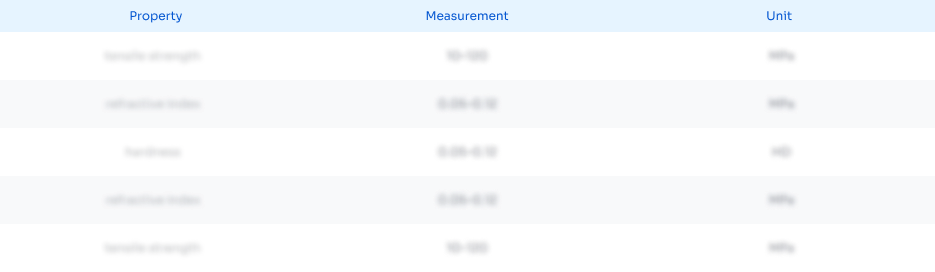
Abstract
Description
Claims
Application Information

- Generate Ideas
- Intellectual Property
- Life Sciences
- Materials
- Tech Scout
- Unparalleled Data Quality
- Higher Quality Content
- 60% Fewer Hallucinations
Browse by: Latest US Patents, China's latest patents, Technical Efficacy Thesaurus, Application Domain, Technology Topic, Popular Technical Reports.
© 2025 PatSnap. All rights reserved.Legal|Privacy policy|Modern Slavery Act Transparency Statement|Sitemap|About US| Contact US: help@patsnap.com