Super-slow hydraulic system for synchro-driven die-forging hydraulic press
A synchronous drive and hydraulic system technology, applied in the field of die forging hydraulic presses, can solve the problems of flow fluctuation of the driving cylinder, destroying the flow rule of the workpiece grains, affecting the quality of the workpiece forming, etc., and achieve the effect of stable flow output.
- Summary
- Abstract
- Description
- Claims
- Application Information
AI Technical Summary
Problems solved by technology
Method used
Image
Examples
Embodiment Construction
[0010] The present invention will be further described below in conjunction with the accompanying drawings.
[0011] see figure 1 and figure 2 , consisting of 5 drive cylinder synchronous drive channels, 1 drive cylinder ultra-slow drive channel, 1 drive cylinder pressure relief channel, 1 return cylinder drain channel and 1 return cylinder liquid inlet channel, 5 drive cylinders synchronously The drive channels are independent of each other, and the flow and pressure of each channel are guaranteed by a separate oil source to realize the driving synchronization of the moving beam during fast forward and slow forward; one drive cylinder super slow drive channel realizes the constant flow of the drive cylinder during the working stage Ultra-slow speed drive; 1 drive cylinder pressure relief channel realizes the rapid unloading of 5 drive cylinders after the hydraulic press is loaded; 1 return cylinder drain channel can control the brake beam in the fast forward, slow forward, ...
PUM
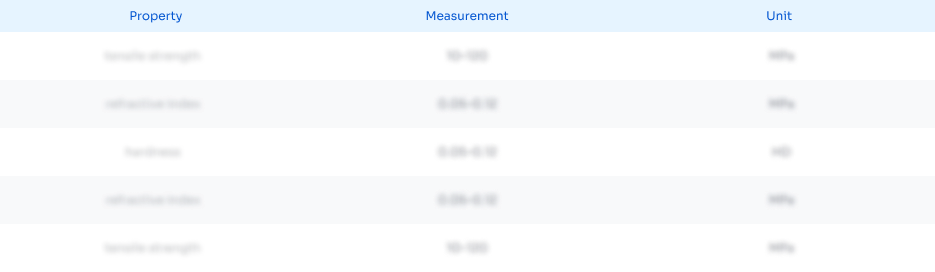
Abstract
Description
Claims
Application Information

- Generate Ideas
- Intellectual Property
- Life Sciences
- Materials
- Tech Scout
- Unparalleled Data Quality
- Higher Quality Content
- 60% Fewer Hallucinations
Browse by: Latest US Patents, China's latest patents, Technical Efficacy Thesaurus, Application Domain, Technology Topic, Popular Technical Reports.
© 2025 PatSnap. All rights reserved.Legal|Privacy policy|Modern Slavery Act Transparency Statement|Sitemap|About US| Contact US: help@patsnap.com