Recycling method of tail gas from pyrolusite reduction and sulfuric acid coproduction in fluidized bed furnace
A technology of tail gas circulation and boiling furnace, applied in manganese sulfate, chemical instruments and methods, sulfur compounds, etc., can solve the problems of poor operating conditions, high labor intensity, long process, etc., to reduce production costs, improve reduction reaction efficiency, and improve operation. good condition
- Summary
- Abstract
- Description
- Claims
- Application Information
AI Technical Summary
Problems solved by technology
Method used
Image
Examples
Embodiment 1
[0032] Mix 500kg sulfur and 250kg pyrolusite (according to the ratio 1:0.5) into the boiling furnace, and blow air into the lower section of the boiling furnace, so that the materials will boil and burn in the boiling furnace under the force of the bottom airflow and the negative pressure on the furnace top Control the temperature of the boiling layer at about 850-950, and control the oxygen content in the lower section of the boiling furnace at about 10%. The sulfur blended in the pyrolusite burns to generate sulfur dioxide, which generates a lot of heat and reduces the manganese dioxide in the pyrolusite to manganese monoxide. The manganese monoxide is directly discharged into a sulfuric acid solution (or electrolytic manganese anolyte) for slurrying and leaching manganese sulfate, and the content of manganese sulfate is determined by conventional methods. The lower furnace gas is deficient in oxygen and contains sublimed sulfur. Blow air into the upper section of the boiling ...
Embodiment 2
[0035] Embodiment 2: The similarities with embodiment 1 will not be described, the difference is:
[0036] 400kg of sulfur and 800kg of pyrolusite (in a ratio of 1:2) are mixed and sent into the boiling furnace, the boiling layer temperature is controlled at 750-850°C, the boiling furnace outlet temperature is 800-850, and the sulfur dioxide concentration at the boiling furnace outlet is 10-13%. The furnace gas is sent to the purification process after dust removal, and the furnace gas is sent to the purification process after dust removal. The sulfur dioxide is catalyzed by a catalyst to form sulfur trioxide, which reacts with water to form sulfuric acid. Part of the unabsorbed furnace gas is used as tail gas and mixed with air. Reconnect to the lower section of the boiling furnace, control the oxygen content at 9.5% by adjusting the tail gas valve, and the ratio of tail gas to air is 1:1.2. The output of manganese monoxide was 458kg, and the manganese utilization rate reached 9...
Embodiment 3
[0037] Embodiment 3: The same parts as in embodiment 1 will not be described, the difference is:
[0038] 400kg of sulfur and 1600kg of pyrolusite (in a ratio of 1:4) are mixed and sent into the boiling furnace, the temperature of the boiling layer is controlled to be 600-700, the temperature of the outlet of the boiling furnace is 700-800, and the concentration of sulfur dioxide at the outlet of the boiling furnace is 10-13%. The furnace gas is sent to the purification process after dust removal, and the furnace gas is sent to the purification process after dust removal. The sulfur dioxide is catalyzed by a catalyst to form sulfur trioxide, which reacts with water to form sulfuric acid. Part of the unabsorbed furnace gas is used as tail gas and mixed with air. Reconnect to the lower section of the boiling furnace, control the oxygen content at 9.8% by adjusting the tail gas valve, and the ratio of tail gas to air is 1:1.4. The output of manganese monoxide was 924kg, and the mang...
PUM
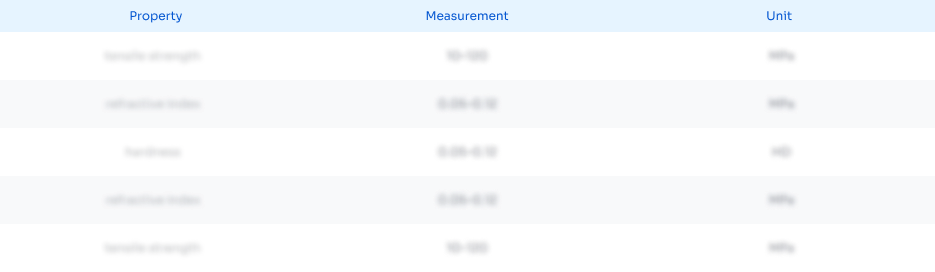
Abstract
Description
Claims
Application Information

- R&D Engineer
- R&D Manager
- IP Professional
- Industry Leading Data Capabilities
- Powerful AI technology
- Patent DNA Extraction
Browse by: Latest US Patents, China's latest patents, Technical Efficacy Thesaurus, Application Domain, Technology Topic, Popular Technical Reports.
© 2024 PatSnap. All rights reserved.Legal|Privacy policy|Modern Slavery Act Transparency Statement|Sitemap|About US| Contact US: help@patsnap.com