Manufacturing process for printing roller multi-depth forme
A manufacturing method and multi-depth technology, applied in the field of printing and dyeing rollers, can solve the problem of single effect and achieve a three-dimensional and layered effect
- Summary
- Abstract
- Description
- Claims
- Application Information
AI Technical Summary
Problems solved by technology
Method used
Examples
Embodiment Construction
[0011] Mother roll plate of the present invention is long 600 millimeters, and diameter is 233.50 millimeters, and mother roller has plated bottom nickel, and the thickness of nickel is 1 silk, and the manufacture method of the present invention is further described below.
[0012] Machining: Machining length of mother roll is 750 mm, diameter is 233.50 mm.
[0013] Copper plating: The thickness of copper plating on one side of the mother roller is 17 wires.
[0014] Grinding: Grinding the copper layer to a plate roll diameter of 233.84 mm, and ensuring a smooth plate surface.
[0015] Manuscript production: Use computer software to make patterns according to customer requirements. During the pattern making process, more points and lines must be used, and the interval between points and lines should be properly controlled to avoid the gap between points and lines being too small. , so that the dots and lines are connected together after the printing is foamed, and there is no...
PUM
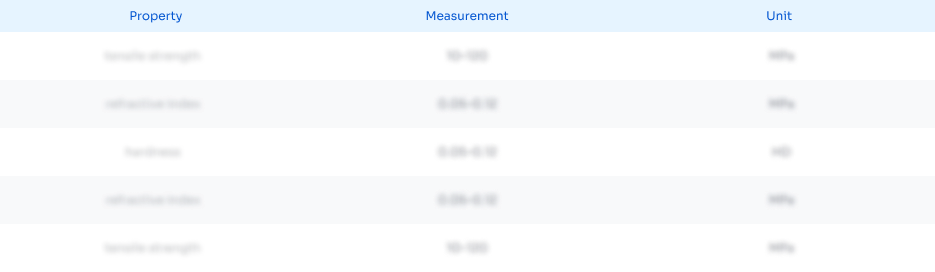
Abstract
Description
Claims
Application Information

- R&D
- Intellectual Property
- Life Sciences
- Materials
- Tech Scout
- Unparalleled Data Quality
- Higher Quality Content
- 60% Fewer Hallucinations
Browse by: Latest US Patents, China's latest patents, Technical Efficacy Thesaurus, Application Domain, Technology Topic, Popular Technical Reports.
© 2025 PatSnap. All rights reserved.Legal|Privacy policy|Modern Slavery Act Transparency Statement|Sitemap|About US| Contact US: help@patsnap.com