O-shaped seal ring rubber sizing material of parallel gate valve end surfaces and preparation method thereof
The technology of O-ring and rubber compound is applied in the field of O-seal rubber compound for the end face of a parallel gate valve and its preparation field, which can solve the problems of expensive raw materials, high cost, relatively high requirements on sealing and corrosion resistance, and Achieve the effect of low material cost, good air tightness and good comprehensive performance
- Summary
- Abstract
- Description
- Claims
- Application Information
AI Technical Summary
Problems solved by technology
Method used
Image
Examples
Embodiment 1
[0031] 1. Raw material preparation:
[0032] Preparation of raw materials for rubber compound:
[0033] Weigh nitrile rubber 3304 90, sulfur 0.4, zinc oxide 5, stearic acid 1.5, antioxidant BHT 1.5, antioxidant RD 1.5, antioxidant 4010Na1.5, microcrystalline wax 3.5, quick press carbon black N660 24, High wear-resistant carbon black N330 63, dioctyl ester 20, magnesium carbonate 12, accelerator M 3.5, accelerator DM 1.5, accelerator PZ 1.5,
[0034] Preparation of raw materials for B rubber compound:
[0035] Weigh polyacrylate rubber 85, silicone rubber 15, zinc stearate 1.5, anti-aging agent RD 2, gelatin T-78 0.5, rhine wax 1.5, quick extruded carbon black 50, quartz powder 10, hydroxyl silicone oil 6, Dilead tetroxide 5, vulcanizing agent TCY 0.8, accelerator Na-22 1-2.
[0036] 2. The method for preparing the rubber compound of the O-ring on the end face of the parallel gate valve comprises the following steps:
[0037] The first step: Prepare A rubber material and B ...
PUM
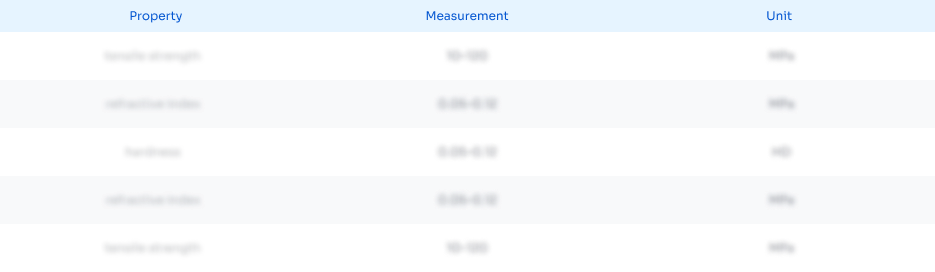
Abstract
Description
Claims
Application Information

- Generate Ideas
- Intellectual Property
- Life Sciences
- Materials
- Tech Scout
- Unparalleled Data Quality
- Higher Quality Content
- 60% Fewer Hallucinations
Browse by: Latest US Patents, China's latest patents, Technical Efficacy Thesaurus, Application Domain, Technology Topic, Popular Technical Reports.
© 2025 PatSnap. All rights reserved.Legal|Privacy policy|Modern Slavery Act Transparency Statement|Sitemap|About US| Contact US: help@patsnap.com