Method for preparing spindle bolster of spinning machine
A spinning machine and spindle foot technology, applied in the field of spindle foot preparation, can solve the problems of low strength, high processing cost of steel spindle foot, low tensile strength, etc., and achieve the effects of low processing cost, saving raw materials and excellent performance
- Summary
- Abstract
- Description
- Claims
- Application Information
AI Technical Summary
Problems solved by technology
Method used
Examples
Embodiment 1
[0017] A preparation method for a spindle foot of a spinning machine spindle, comprising the following steps:
[0018] 1) Powder proportioning and mixing: the raw material powders used are composed of: -200 mesh electrolytic copper powder 0.8%, -200 mesh electrolytic nickel powder 0.8%, -200 mesh electrolytic chromium powder 1.5%, -120 mesh 0.6% of graphite powder, 0.3% of -200 mesh electrolytic manganese powder, and the balance is -200 mesh of reduced iron powder; add an appropriate amount of pressing lubricant to the above powder, and then put it into a mixer and mix for 5 hours to prepare a mixed powder;
[0019] 2) Compression: Press the mixed powder prepared in step 1) in a molding die to form an ingot foot compact on a hydraulic press, and the pressing pressure is 550 MPa;
[0020] 3) Sintering: Sinter the ingot foot compact obtained in step 2) in a sintering furnace, and the sintering atmosphere is H 2 , the sintering temperature is 1150°C, and the sintering time is 4...
Embodiment 2
[0023] A preparation method for a spindle foot of a spinning machine spindle, comprising the following steps:
[0024] 1) Powder proportioning and mixing: The raw material powders used are composed of: -200 mesh electrolytic copper powder 1.2%, -200 mesh electrolytic nickel powder 0.2%, -200 mesh electrolytic chromium powder 2.2%, -120 mesh 0.4% of graphite powder, 0.8% of -200 mesh electrolytic manganese powder, and the balance is -200 mesh of reduced iron powder; add an appropriate amount of pressing lubricant to the above powder, and then put it into a mixer and mix for 3 hours to prepare a mixed powder;
[0025] 2) Pressing: press the mixed powder prepared in step 1) in a molding die on a hydraulic press to form an ingot foot compact, and the pressing pressure is 600MPa;
[0026] 3) Sintering: Sinter the ingot foot compact obtained in step 2) in a sintering furnace, the sintering atmosphere is H2, the sintering temperature is 1165°C, and the sintering time is 3.5 hours; ...
Embodiment 3
[0029] A preparation method for a spindle foot of a spinning machine spindle, comprising the following steps:
[0030] 1) Powder proportioning and mixing: The raw material powders used are composed of: -200 mesh electrolytic copper powder 1.0%, -200 mesh electrolytic nickel powder 0.6%, -200 mesh electrolytic chromium powder 1.8%, -120 mesh 0.5% of graphite powder, 0.5% of -200 mesh electrolytic manganese powder, and the balance is -200 mesh of reduced iron powder; add an appropriate amount of pressing lubricant to the above powder, and then put it into a mixer and mix for 4 hours to prepare a mixed powder;
[0031] 2) Pressing: press the mixed powder prepared in step 1) in a molding die on a hydraulic press to form an ingot foot compact, and the pressing pressure is 580 MPa;
[0032] 3) Sintering: Sinter the ingot foot compact obtained in step 2) in a sintering furnace, and the sintering atmosphere is H 2 , the sintering temperature is 1160°C, and the sintering time is 3.5 ...
PUM
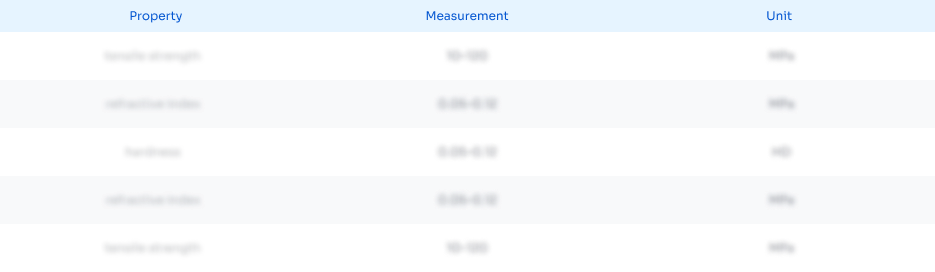
Abstract
Description
Claims
Application Information

- R&D Engineer
- R&D Manager
- IP Professional
- Industry Leading Data Capabilities
- Powerful AI technology
- Patent DNA Extraction
Browse by: Latest US Patents, China's latest patents, Technical Efficacy Thesaurus, Application Domain, Technology Topic, Popular Technical Reports.
© 2024 PatSnap. All rights reserved.Legal|Privacy policy|Modern Slavery Act Transparency Statement|Sitemap|About US| Contact US: help@patsnap.com