Heat sink with needle rib-recessed composite array and method for arranging needle rib-recessed composite array
A composite array and pin-fin technology, applied in the field of heat dissipation devices, can solve the problems of increased power consumption and noise of pumps or fans, large flow resistance of cooling fluid, increased flow loss, etc., to reduce weight, reduce power consumption, and reduce density Effect
- Summary
- Abstract
- Description
- Claims
- Application Information
AI Technical Summary
Problems solved by technology
Method used
Image
Examples
specific Embodiment 1
[0035] Such as figure 1 As shown, the pin fin-recess composite array heat sink 20 in this embodiment includes: a base plate 22 , a plurality of pin fins 16 , cooling channels 14 and a top plate 10 . The wall surface 26 of the substrate 22 of the heat sink is in close contact with the surface of the heat-generating device, so as to receive heat from the surface of the device. This heat is then carried away by the cooling fluid in the cooling channels 14 . The base plate 22 and the top plate 10 can be coupled together through the holes 23 by fasteners.
[0036] The pin fins 16 are formed on the inner wall surface 24 of the substrate by integral milling or brazing or casting or other processing methods. Both the pin fins 16 and the substrate 22 are made of high thermal conductivity materials, such as copper, aluminum or AlSiC. The pin rib 16 has a columnar shape with a circular cross section. Of course, the pin fins in the present invention can also be configured to have a rh...
specific Embodiment 2
[0039] Figure 4 and Figure 5 Shown is a fin-and-dimple array heat sink 20 having another arrangement. and figure 2 The difference between the shown pin fin-depression array heat sink is that the depression 18 is not only arranged on the inner wall surface 24 of the substrate at the minimum flow section between the transverse pin fins 16, but also between every two columns of pin fins 16 in the longitudinal direction. There is a column of depressions 18 . The recesses 18 are staggeredly arranged on the inner wall surface 24 of the substrate. and figure 2 Compared with the pin fin-recess array arrangement scheme shown, Figure 4 In the shown arrangement the base plate inner wall 24 has more depressions. Such as Figure 6 As shown, when the fluid flows through the array of pin fins 16 and depressions 18, strong eddy currents 15 are generated, and the interaction between the eddy currents can significantly further enhance the turbulent flow mixing near the inner wall su...
specific Embodiment 3
[0041] Figure 7 It is described that the fin-depression array heat sink 20 simultaneously dissipates heat from two devices. In this embodiment, the cooling channel 14 is bounded between the upper and lower base plates 22 . The inner wall surfaces 24 of the two substrates are processed with pin ribs 16 and recesses 18 . The pin rib 16 is connected to the upper and lower base plates 22 . In this arrangement, therefore, there is no top plate 10 . exist Figure 7 In the illustrated embodiment, the configuration scheme of pin fins and depressions in the cooling channel 14 between the two base plates 22 is the same as that of figure 2 or Figure 4 Similar to what is shown. The cooling fluid flows into the heat sink to convectively cool the upper and lower substrates 22 . Obviously, such a heat dissipation solution is very compact, which is beneficial to saving space, weight and cost, and is very beneficial to the cooling design of aviation and aerospace electronic equipment...
PUM
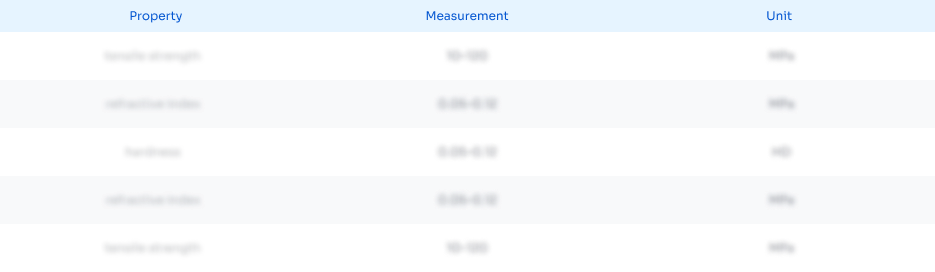
Abstract
Description
Claims
Application Information

- Generate Ideas
- Intellectual Property
- Life Sciences
- Materials
- Tech Scout
- Unparalleled Data Quality
- Higher Quality Content
- 60% Fewer Hallucinations
Browse by: Latest US Patents, China's latest patents, Technical Efficacy Thesaurus, Application Domain, Technology Topic, Popular Technical Reports.
© 2025 PatSnap. All rights reserved.Legal|Privacy policy|Modern Slavery Act Transparency Statement|Sitemap|About US| Contact US: help@patsnap.com