Extrusion casted Al-Zn alloy material with high toughness
A technology of squeeze casting and alloy materials, applied in the field of aluminum alloy materials, to achieve the effects of good casting formability, good plasticity and flow properties, and high strength
- Summary
- Abstract
- Description
- Claims
- Application Information
AI Technical Summary
Problems solved by technology
Method used
Image
Examples
Embodiment 1
[0020] The extrusion casting Al-Zn series alloy material of the present invention adopts extrusion casting technology, and adopts solid solution treatment+artificial aging technology to prepare, and steps and technology thereof are as follows:
[0021] Step 1: Ingredients
[0022]
[0023]
[0024] Step 2: Smelting
[0025] The alloy is smelted in a graphite crucible. Preheat the crucible to dark red before smelting. Add pure aluminum, Al-50Cu intermediate alloy, aluminum-zirconium alloy when the furnace temperature is 300-400°C, and add pure magnesium and pure zinc when the furnace temperature is 700°C. , Add aluminum-titanium-boron alloy and aluminum-rare-earth alloy at 720°C. After it is completely melted, refine and degas it, let it stand for a few minutes to remove slag, stir well and pour at 720°C.
[0026] Step Three: Squeeze Casting
[0027] Squeeze casting press is 100 tons four-column hydraulic press, which is carried out on the direct extrusion casting mold....
Embodiment 2
[0034] The extrusion casting Al-Zn series alloy material of the present invention adopts extrusion casting technology, and adopts solid solution treatment+artificial aging technology to prepare, and steps and technology thereof are as follows:
[0035] Step 1: Ingredients
[0036]
[0037]
[0038] Step 2: Melting, Step 3: Squeeze Casting, Step 4: Heat Treatment
[0039] Same as Embodiment 1.
[0040] The squeeze casting Al-Zn alloy material obtained through the above steps has been tested for its main components and their mass percentages: alloy material zinc 7.00%, magnesium 2.80%, copper 2.00%, titanium 0.15%, boron 0.03%, zirconium 0.15%, mixed rare earth 0.10%, the rest is aluminum and unavoidable impurities, of which iron is 0.20%, silicon is 0.10%. The mechanical properties of the alloy material in this example under different specific pressures are shown in Table 2.
[0041] Table 2 Mechanical properties of alloys under different extrusion ratios
[0042] ...
Embodiment 3
[0044] Step 1: Ingredients
[0045]
[0046] Step 2: Melting, Step 3: Squeeze Casting, Step 4: Heat Treatment
[0047] Same as Embodiment 1.
[0048] The extrusion casting Al-Zn alloy material obtained through the above steps has been tested for its main components and mass percentages: 7.30% zinc, 2.90% magnesium, 1.90% copper, 0.20% titanium, 0.04% boron, and 0.20% zirconium , mixed rare earth 0.15%, the rest is aluminum and unavoidable impurities, of which iron is 0.20%, silicon is 0.10%. The mechanical properties of the alloy material in this example under different specific pressures are shown in Table 3.
[0049] Table 3 Mechanical properties of alloys under different extrusion ratios
[0050] Extrusion specific pressure
PUM
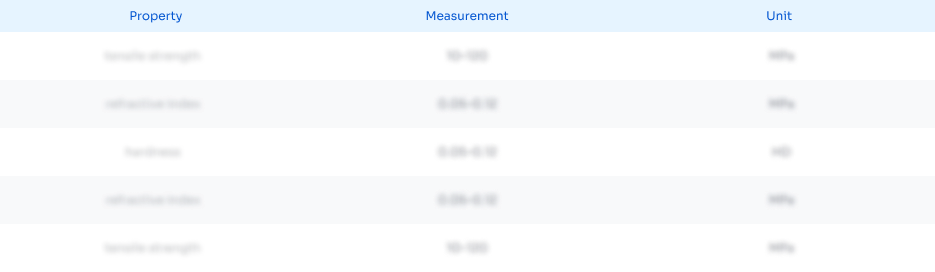
Abstract
Description
Claims
Application Information

- R&D
- Intellectual Property
- Life Sciences
- Materials
- Tech Scout
- Unparalleled Data Quality
- Higher Quality Content
- 60% Fewer Hallucinations
Browse by: Latest US Patents, China's latest patents, Technical Efficacy Thesaurus, Application Domain, Technology Topic, Popular Technical Reports.
© 2025 PatSnap. All rights reserved.Legal|Privacy policy|Modern Slavery Act Transparency Statement|Sitemap|About US| Contact US: help@patsnap.com