High-mechanical strength carbon-containing pellets for blast furnace and production method for high-mechanical strength carbon-containing pellets
A mechanical strength and blast furnace technology, applied in the field of high mechanical strength carbon-containing pellets, can solve the problems of increased production cost, high carbon material addition, and low strength of finished balls, so as to save energy, improve mine strength, reduce The effect of focal ratio
- Summary
- Abstract
- Description
- Claims
- Application Information
AI Technical Summary
Problems solved by technology
Method used
Image
Examples
Embodiment 1
[0024] Weigh according to the ratio given in Table 1 and preliminarily dry mix for 10 minutes, then spray water to wet it, so that the moisture content of the mixture is controlled at 8.1%. The disc pelletizer prepares green balls, and the obtained green balls are screened to obtain Qualified green balls are then roasted in a belt machine at a roasting temperature of 1250°C for a roasting time of 12 minutes to finally obtain finished balls.
Embodiment 2
[0026] Weigh according to the proportion given in Table 1 and preliminarily dry mix for 15 minutes, then spray water to wet, so that the moisture content of the mixture is controlled at 8.5%, and after 60 minutes of stuffing, the The disc pelletizer prepares green balls, and the obtained green balls are screened to obtain Qualified raw balls are then roasted in a chain grate machine-rotary kiln at a roasting temperature of 1280°C for a roasting time of 10 minutes to finally obtain finished balls.
Embodiment 3
[0028] Weigh according to the proportion given in Table 1 and preliminarily dry mix for 15 minutes, then spray water to wet it, so that the moisture content of the mixture is controlled at 9%, and after 60 minutes of stuffing, the The disc pelletizer prepares green balls, and the obtained green balls are screened to obtain Qualified raw balls are then roasted in a chain grate machine-rotary kiln at a roasting temperature of 1300°C for a roasting time of 13 minutes to finally obtain finished balls.
PUM
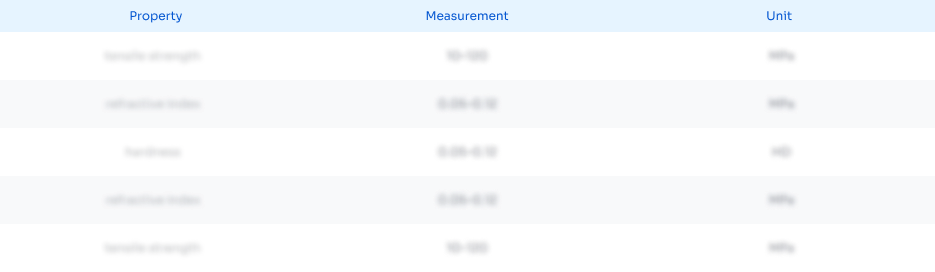
Abstract
Description
Claims
Application Information

- R&D
- Intellectual Property
- Life Sciences
- Materials
- Tech Scout
- Unparalleled Data Quality
- Higher Quality Content
- 60% Fewer Hallucinations
Browse by: Latest US Patents, China's latest patents, Technical Efficacy Thesaurus, Application Domain, Technology Topic, Popular Technical Reports.
© 2025 PatSnap. All rights reserved.Legal|Privacy policy|Modern Slavery Act Transparency Statement|Sitemap|About US| Contact US: help@patsnap.com