Comprehensive processing process for sintering smoke gas
A technology for comprehensive treatment of sintering flue gas, which is applied in waste heat treatment, treatment of discharged materials, improvement of process efficiency, etc., can solve the problems of inability to recover and utilize waste heat of sintering flue gas, high operating costs, and huge equipment, and achieve The effect of resource utilization, increasing outlet air temperature, and saving equipment costs
- Summary
- Abstract
- Description
- Claims
- Application Information
AI Technical Summary
Problems solved by technology
Method used
Image
Examples
Embodiment Construction
[0018] The specific implementation manners of the present invention will be described in detail below in conjunction with the accompanying drawings.
[0019] As shown in the figure, it is a schematic structural diagram of the cement production equipment used in the embodiment of the sintering flue gas comprehensive treatment process of the present invention. The flue gas comprehensive treatment process of this embodiment includes the following steps:
[0020] 1) Waste heat recovery: part of the sintering flue gas with low dioxin concentration enters the hot blast furnace 13 of the rotary kiln 12 as combustion air, and part of it enters the grate cooler 3 as cooling gas to cool the clinker. 3. The high-temperature flue gas that comes out enters the rotary kiln 12 and enters the calciner 11 from the middle part of the calciner 11 respectively as a combustion-supporting gas, and the high-temperature flue gas burned by the rotary kiln 12 enters the calciner 11 from the bottom of th...
PUM
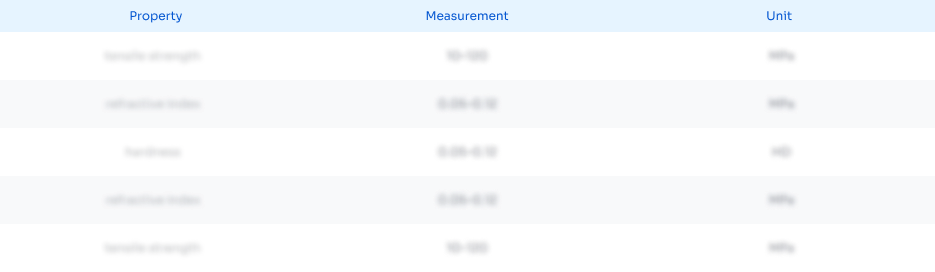
Abstract
Description
Claims
Application Information

- Generate Ideas
- Intellectual Property
- Life Sciences
- Materials
- Tech Scout
- Unparalleled Data Quality
- Higher Quality Content
- 60% Fewer Hallucinations
Browse by: Latest US Patents, China's latest patents, Technical Efficacy Thesaurus, Application Domain, Technology Topic, Popular Technical Reports.
© 2025 PatSnap. All rights reserved.Legal|Privacy policy|Modern Slavery Act Transparency Statement|Sitemap|About US| Contact US: help@patsnap.com