Process flow for carrying out high-pressure and low-pressure adsorption treatments on polyolefin tail gas
A high-pressure polyolefin and process technology, applied in the direction of dispersed particle separation, chemical instruments and methods, separation methods, etc., can solve the problem of low hydrocarbon concentration in hydrocarbon-rich gas, no low-pressure tail gas recovery treatment, excluding polypropylene tail gas recovery treatment, etc. problem, to achieve the effect of pollutant reduction
- Summary
- Abstract
- Description
- Claims
- Application Information
AI Technical Summary
Problems solved by technology
Method used
Image
Examples
Embodiment
[0042] Low-pressure tail gas flow rate of 1500Nm from a polyolefin plant 3 / h, temperature 35°C, pressure 0.11MPa (absolute), high-pressure tail gas flow rate 1000Nm 3 / h, temperature 35°C, pressure 1.1MPa (absolute), the raw material contains 776kg / h of non-methane hydrocarbons, and the tail gas composition is shown in Table-1:
[0043] Table-1 Composition of Raw Gas in Examples
[0044]
[0045] The polyolefin tail gas recovery device for processing the above-mentioned high and low pressure polyolefin tail gas has 4 adsorption beds filled with activated carbon, numbered A, B, C, and D respectively. Table-2 is the work schedule of the adsorption beds:
[0046] Table-2 Example adsorption bed work schedule
[0047]
[0048] The following takes A adsorption bed as an example to explain the entire pressure swing adsorption process.
[0049] Assuming that the adsorption bed A in the pressure swing adsorption device is in the first stage of low-pressure adsorption (LA) at ...
PUM
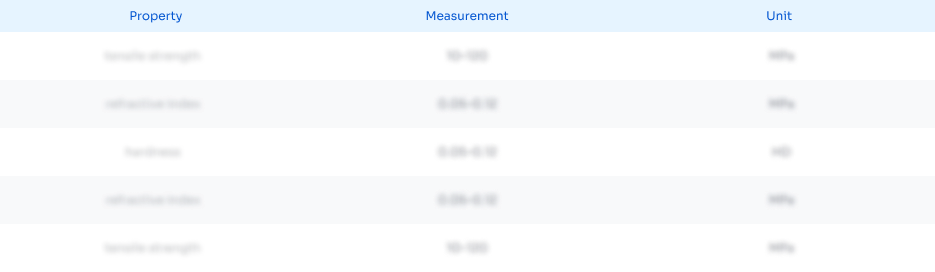
Abstract
Description
Claims
Application Information

- R&D
- Intellectual Property
- Life Sciences
- Materials
- Tech Scout
- Unparalleled Data Quality
- Higher Quality Content
- 60% Fewer Hallucinations
Browse by: Latest US Patents, China's latest patents, Technical Efficacy Thesaurus, Application Domain, Technology Topic, Popular Technical Reports.
© 2025 PatSnap. All rights reserved.Legal|Privacy policy|Modern Slavery Act Transparency Statement|Sitemap|About US| Contact US: help@patsnap.com